Injection moulding is a complex operation requiring both hardware (the moulding machine and mould) and software (for manipulating the moulding machine and designing moulds). A simplified installation guide for an injection moulding system.
Note that particulars may differ based on the type of machine, mould, and material with which you’re working.
Step 1: Selection of the Injection Molding Machine
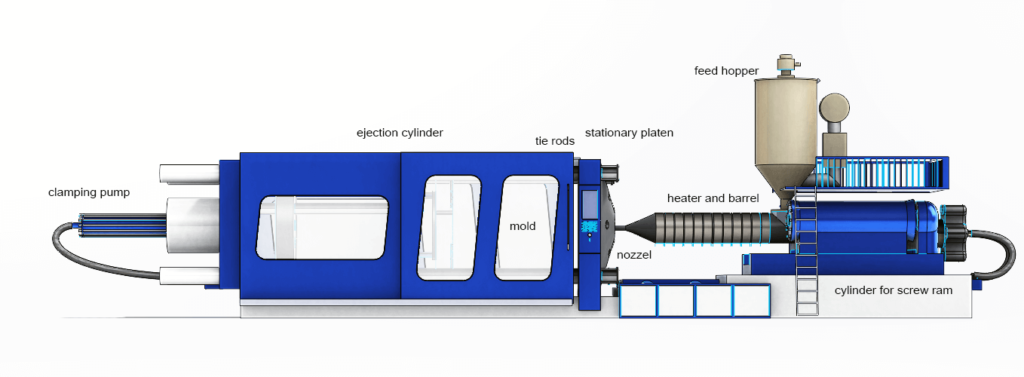
You need to choose a machine suitable for the type and size of products you intend to manufacture. This includes considering factors such as:
- The Power of Clamping Force
In injection molding, the clamping force is the powerhouse that ensures the mold remains securely closed during the injection process. Measured in tons, this force guarantees the mold’s close, preventing any misalignments or openings that could compromise the quality of the final product,like flash.
Below is the clamping force range for different types of parts:
Small parts: 5-50 tons,
Medium-sized parts: 50-200 tons,
Large parts: 200-1,000 tons,
Very large parts: 1,000+ tons
- Shot Size: A Vital Component
The shot size refers to the maximum volume of plastic that the injection molding machine can proficiently introduce into the mold within a single cycle. It’s a crucial determinant of the part’s size and weight, typically quantified in either grams or ounces. The shot size directly impacts the physical attributes of the end product, underscoring its importance in the molding process.
Product shot size = spruce + runner + product + shrinkage
- General Resins (PPPE, PS,PP,PE)Size injection unit for 20% to 80% of shot capacity
- Engineered Resins (ABS, PC POM PA):Size injection unit for 30% to 50% of shot capacity
A case:
The formula is as follows:
Shot size = (mould volume) * density x (desired part weight)
For example, if the injection mould has a volume of 1500cc, the material density is 0.92g/cc(PP,PE), and the part weight is 70 grams, the shot size would be:
Shot size = 1500cc x 0.92g/cc x 70g = 96,600 cubic millimeters (mm3)
- Influence of Injection Pressure
Injection pressure is another critical aspect, as it drives the molten plastic into the cavity of the mold. This force, expressed in psi or bar, must be optimally calibrated. An appropriately set injection pressure ensures smooth and complete filling of the mold, avoiding potential defects that could mar the final product.
- The Importance of Tie Bar Spacing
Tie bar spacing is the distance between the horizontal and vertical bars holding the mold, is a fundamental characteristic of the machine itself. This spacing must be large enough to install the mold. The consideration of tie bar spacing ensures compatibility between the machine and mold, facilitating an efficient and smooth operation.
Understanding these key parameters is crucial in optimizing the injection molding process, leading to the production of high-quality, uniform parts. This insight into the intricacies of injection molding provides a robust foundation for making informed decisions in this field, ensuring superior results every time.
Step 2: Machine Installation
Assuring optimal performance and longevity for any machine is of utmost importance to its overall success and lifespan. By following some essential guidelines, creating an environment which fosters efficiency, safety, and productivity is easy. Important considerations when installing your machine, with emphasis placed upon providing a clean, well ventilated, well-lit space – key factors will enable informed decisions that maximize its potential!
- Choosing an Ideal Location: Cleanliness and Ventilation
To ensure smooth operations of your machine, selecting an optimal location is of great importance. Achieve this through cleaning to keep out dust or other particles that could compromise its components causing malfunction or reduced performance; while proper ventilation ensures air circulates effectively so as to minimize heat accumulation which could hamper performance negatively; in doing this you create the optimal space for its smooth functioning.
- Sufficient Space for Machine, Materials, and Products
Ensuring there is enough room for all the pieces involved is key for efficient workflow. Allowing sufficient access to machines, material handling needs and production processes as well as efficient movement during production is made simpler with adequate planning of available space – this also reduces accidents or potential damages caused to machinery as a result of insufficient allocations of it. By optimizing this area you enhance productivity as well as reduce accidents caused by damage to machines or nearby objects that might arise as a result.
- Ensuring Floor Stability
Your weight-bearing machine requires a strong foundation in order to function safely. In order to safeguard its functioning and avoid potential missteps or malfunction, ensure its flooring can absorb vibrations caused by running; an assessment of load bearing capacity will help identify structural issues before they lead to machine breakdown or complete structural collapse.
- Place Your Machine Near Essential Utilities
In order to achieve maximum operational efficiencies and streamline production processes, locating your machine near essential utilities like electricity, cooling water and compressed air may help maximize operational efficiencies as well as ensure smooth production without interruption or hindrance. Doing this will save both time and effort when connecting these utilities directly to the machine as well as ensure no production disruption or hindrance occurs.
- Prioritizing Electrical Safety
To prevent electrical hazards and protect both personnel and machines from potential electrical accidents, grounding of machines should take top priority. Effective grounding measures reduce electrical malfunction risks while guarding against damages to both machines as well as potential harm caused to operators.
- Hydraulic Systems and Additional Requirements
Machines which utilize hydraulic systems must also connect them with an oil reservoir and cooling system in order for proper functioning and longevity of performance to take place. By meeting each specific system requirement diligently, optimal performance and longevity will result.
Step 3: Mold Installation
- Designing and Installing High-Quality Molds for Maximum Performance
Mold design and manufacturing require great precision and expertise, using advanced CAD software for design. In order to guarantee seamless integration within machine tie bar spacing and with sufficient strength to withstand clamping force. To achieve optimal performance it’s vital that high-quality mold design and installation takes place efficiently and on schedule.
- Thorough Cleaning for Impeccable Results
Before installation, it is critical that a mold be thoroughly cleaned to ensure no contamination or debris are hindering its performance or detracting from final quality of final product. A clean mold contributes significantly towards efficient manufacturing operations as a whole and long term success of manufacturing process.
- Careful Installation for Seamless Operation
Mold installation requires careful handling in order to avoid damage or misalignment during its placement into a machine, using either a crane or reliable lifting device with precision and care. Once loaded into its intended destination machine, attention must be given to ensure optimal functionality by aligning and fastening it securely during production processes.
- Integration of Utilities for Enhanced Performance
In order to optimize a mold’s efficiency, connecting any necessary utilities – like cooling lines,hydraulic cylinder and ejector pins- is of vital importance. Cooling lines help regulate production temperatures during production to prevent overheating while protecting product quality while ejector pins assist with efficient product ejection from the mold. By connecting everything properly, molds can operate seamlessly to deliver consistent and exceptional results every time.
Step 4: Machine Setup and Calibration
The key factor in achieving optimal operation of injection molding machines lies in fine tuning their various components such as temperature, pressure and cycle time settings based on plastic material used and product/mold specifications.
- Harnessing the Power of Control Software
Control software included in modern injection molding machines enables precise parameter setting making operations management easier for operators.
The control software could either be specifically designed for the machines unique design or general purpose molding software that suits a range of machine models. Testing of machine functionality before full production runs is crucial in ensuring operational efficiency.
- Test Cycles: Ensuring Operational Efficiency
Prior to commencing the main production runs operators should conduct several test cycles with their machines. This helps assess performance according to expectations and reveals any discrepancies regarding parameters that could impede optimal performance.
Step 5: Operator Training
To ensure operators can efficiently utilize machines, it is vital for them to undergo comprehensive training that addresses both safe operation and routine issues. By developing such essential skills, operators not only reduce risks such as accidents and injuries but can also enhance overall efficiency and productivity.
- Troubleshooting Techniques: Addressing Common Problems
Operators must possess the skill sets needed to quickly detect and resolve common machine operational problems that might occur in order to ensure optimal production workflow and minimize downtime, thus keeping production on schedule without unnecessary delays in production.
- Quality Control Mastery: Ensuring Flawless Finished Products
Operators must not only master machine operations but must also become adept in quality control procedures to ensure the finished products adhere to company and customer standards and expectations. This involves inspecting each item thoroughly for defects or inconsistencies before understanding how best to address issues that are identified – this helps operators ensure end products conform to company and customer standards and expectations. By strictly adhering to quality control guidelines, operators can guarantee end products meet company and customer standards respectively.
- Seamless Integration of Training and Real-World Application
When operators receive proper machine operation, troubleshooting, and quality control training they become invaluable assets during production processes. Their speedy responses to challenges quickly address quality standards are instrumental to smooth workflow and consistently outstanding output by companies investing in such training programs – but more than this they provide companies an edge against rivals as well.
step 6. Safety Precautions
Adherence to manufacturer directives regarding user safety is of utmost importance, as these instructions have been created by experts keeping in mind various risks involved and should not be disregarded lightly.
- The Imperative Role of Personal Protective Equipment (PPE)
Personal Protective Equipment (PPE) is essential to machinery operations. Users should wear all required PPE, such as safety goggles, heat resistant mitts and auditory protection gear, for protection. Wearing these pieces serves as the first line of defense against potential harm – always remember: PPE you wear can make all the difference when it comes to avoiding accidents!
- The Necessity of Regular Machine Inspection and Maintenance
Assuring the optimal working condition for your machine is key to protecting it against mishaps or malfunctions that could potentially arise, as routine checks and timely maintenance not only extend its lifespan but can reduce accidents significantly. Ensuring its healthiness goes far beyond being just preventive; rather it should serve as proactive measure toward increasing both safety and productivity.
- Making Safety a Priority
In conclusion, it’s vitally important that safety remains top of mind at all times. Complying with manufacturer recommendations, wearing adequate PPE and conducting regular machine upkeep are all vital pillars of operational safety that need to be considered an integral part of everyday routine for creating an ideal working environment and efficient business operations.
By embedding safety practices as part of daily practices you can foster an atmosphere that prioritizes safe practices within each step taken – cultivate a culture of safety so every decision taken conforms with best safety practices set in stone by establishing best safety practices throughout.