what is injection molding of plastics
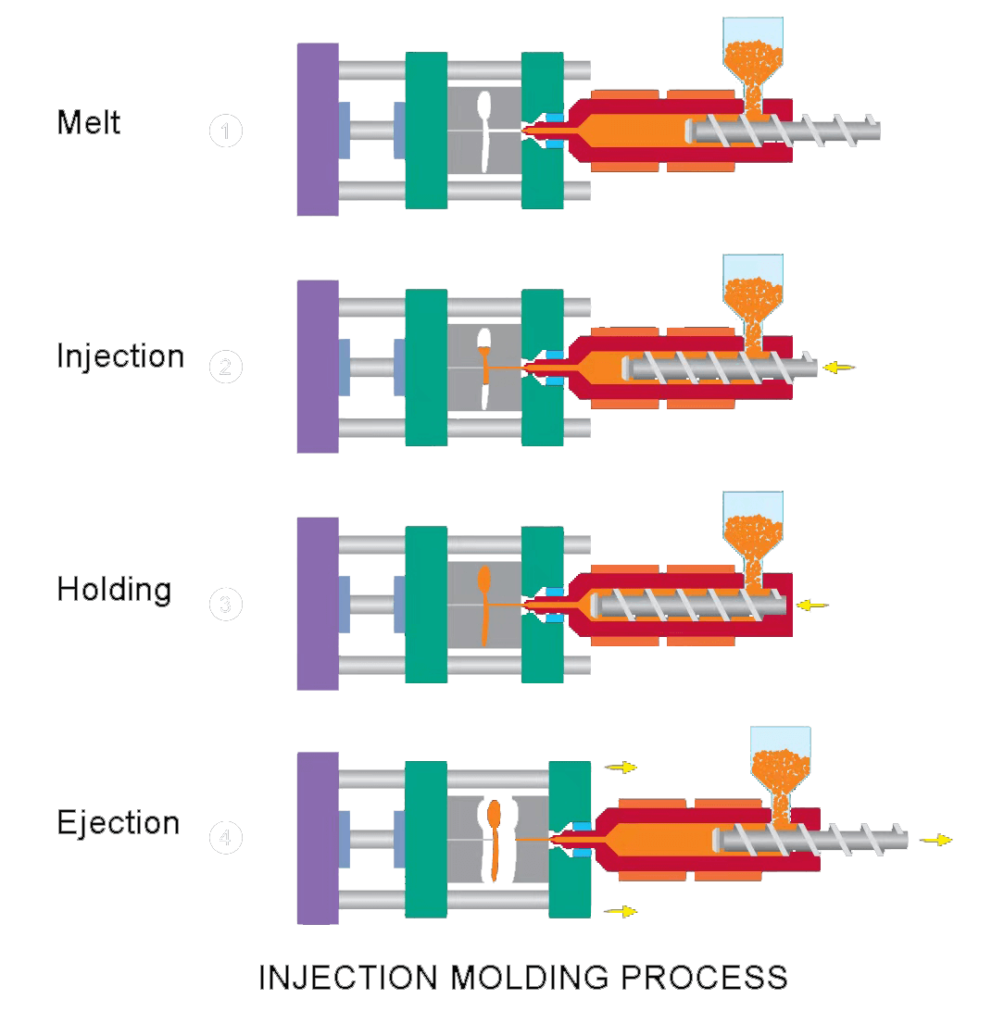
The process of injection molding of plastics involves the usage of molds to create parts through material injection. The plastic manufacturing industry uses this method for component creation because it delivers precision results and high efficiency together with the ability to create intricate shapes. Manufacturers in automotive, consumer goods, and medical device sectors prefer this method because it combines cost efficiency with scalability.
The Cornerstone of Modern Manufacturing
This guide provides an interactive exploration of plastic injection molding, a foundational process for producing complex plastic parts at scale.
Unmatched Versatility
Enables the production of parts with intricate geometries, making it essential for industries from automotive to medical.
Cost-Effective at Scale
While initial tooling is a significant investment, the low cost-per-part in high-volume runs makes it highly economical.
Material Diversity
Compatible with a vast array of thermoplastic and thermoset polymers, allowing for tailored part properties.
The Injection Molding Cycle
The injection molding process is a sequence of events that repeats to produce parts efficiently. Click on each stage below to learn more.
Anatomy of the Machine
An injection molding machine is a sophisticated blend of high-force mechanics and precision control.
Injection Unit
Clamping Unit
The Heart of the Process: Mold Design
The mold is a precision-engineered tool that dictates the final part's shape, quality, and finish.
Uniform Wall Thickness
The most important rule. Uniform walls promote even cooling and shrinkage, preventing defects like warpage and sink marks.
Draft Angles
A slight taper (1-2° typical) on vertical walls. This is essential for allowing the part to be easily ejected from the mold.
Cooling Channels
A network of channels within the mold that circulates coolant. Efficient cooling is key to reducing cycle time.
Venting
Tiny channels that allow trapped air to escape as molten plastic fills the cavity.
Gate & Runner System
The pathway for plastic to travel from the nozzle to the part cavity.
Ejection System
The mechanism that pushes the finished part out of the mold.
Materials Explorer
The choice of plastic is critical, dictating a part's strength, flexibility, temperature resistance, and cost.
Defect Troubleshooter
Even in a controlled process, defects can occur. Click on a common defect below to see its typical causes and solutions.
How Does Injection Molding Compare?
Injection molding excels at high-volume production of solid parts, but other manufacturing processes are better suited for different needs.
The Future of Injection Molding
While a mature technology, injection molding is continuously evolving.
Smart Manufacturing (IIoT)
Sensors in machines and molds provide real-time data for predictive maintenance and quality assurance.
Conformal Cooling
Using 3D printing to create cooling channels that perfectly follow the part's shape.
Multi-Material & In-Mold Decoration
Combining different plastics or embedding decorative labels in a single step.
Sustainability Focus
A major push towards using more recycled and bio-based plastics.
Steps in the Injection Molding of plastics Process
- Heating Plastic Pellets: The first step involves heating plastic pellets within a hopper until they turn into a liquid state.
- Injection into the Mold: Molten plastic receives high-pressure injection into a mold, through which the cavity gets filled.
- Cooling Treatment: The mold receives cooling treatment after plastic solidification to create the desired part shape.
- Mold Opening: The finished part becomes available after the mold opens when it reaches cooling temperature.
- Finishing Operations: Additional finishing operations, including trimming and painting, are used to finalize the part after production.
Today, injection molding is one of the most widely used ways for building plastic products. It allows a plastic part to be made entirely from a single cycle. Elastomers, duroplast, and elastomers can all be used .
A process for injection molding
The injection molding process begins with small, uniform raw plastic pellets, which are gravity-fed into an injection cylinder. Here, heat tape and the friction from a rotating screw melt the plastic. This molten plastic, precisely measured for one cycle, is then injected under high pressure into a mold, which is the negative shape of the final part.
The process cycle consists of several key stages: filling, injection, packing, holding, cooling, and de-molding. During the filling stage, the screw plasticizes the pellets and moves them into a pre-injection chamber. Critical parameters include cylinder temperature (e.g., 270°C for PMMA, 180°C for PE), screw speed, and back pressure, which ensures a uniform mix.
Next, the injection stage drives the screw forward, forcing the molten plastic into the mold cavity. Injection speed and pressure are vital, influencing the part’s surface finish and structural integrity. After the mold is filled, packing pressure is applied to compensate for the material’s shrinkage as it cools. This is typically 30-50% of the injection pressure. This is followed by holding pressure, which maintains pressure until the gate—the entry point to the mold cavity—freezes, preventing material from flowing back out.
Cooling, which occurs concurrently with the packing and holding phases, solidifies the plastic part. Coolant circulates through channels in the mold to remove heat. The cooling time is primarily determined by the part’s thickest wall section. Once the part is sufficiently rigid, the ejection phase begins. Ejector pins, sleeves, or plates carefully push the finished part out of the mold without causing damage. The mold design and part geometry dictate the most suitable ejection method to ensure a clean release.
Injection molding design tips
It is possible to make simple to extremely complicated injection molded plastic parts, as well as millions of identical items, thanks to the scalability and uniformity of the process. Tool building and maintenance are expensive, and changing tools is a challenge.
Injection molded parts: maximize their benefits
- Consistency is key. Make sure your walls are the same thickness throughout your part. Walls should be 2-3mm thick on average. Standard injection molding processes recommend a minimum of 1mm and a maximum of 4mm.
- Smooth trumps sharp. Smooth out wall transitions whenever possible.
- Draft. A draft angle can cause design challenges in your part. Adding a draft angle to your faces is helpful for releasing the part from the tool, but it can also cause problems, specifically with mate parts. On untextured core surfaces and at least three degrees on textured cavity surfaces, a minimum draft angle of one degree is recommended.
- If possible, stay away from surfaces with zero draft. In the case of a zero-draft area, you should aim to limit it to just a portion of the face, rather than the entire surface.
- Keep it simple. Attempt to prevent undercutting (forming an area that cannot be shaped simply by opening and closing the tool). When simple won’t work, lifter and slides allow features to be formed that are undercuts in the main pull direction. If so, leave at least 2 to 3 times the width of the feature to allow the lifter or slide to travel.
- Flow from thick to thin. Plastic will flow through features better if it flows from thicker to thinner walls beginning at the gate (where the plastic flows into the part to fill it).
- It is bad to have sinks (densities on surfaces caused by thicker sections of plastic slowing down as they cool). It is important to follow these guidelines in order to minimize or eliminate the appearance of blemishes on cosmetic surfaces:
- Make sure that important cosmetic surfaces do not have gates, ribs, screw bosses, etc. on the backside;
- There should be three times less rib height than wall thickness;
- 60% or less of the wall thickness should be used for rib bases.
- Territories are defined by datums. To establish the interface and interaction between parts, use datums (features that serve as reference points for the parts). When a design intent is matched to a datum structure, a product can function properly.
- There is nothing wrong with interrogation. In DFM (Design for Manufacturing) reports, the molder communicates his understanding of the design, especially in regards to pin locations, gate locations, and parting lines (which could affect how parts interact). Interrogate the design by using inspection reports.
- Create prototypes often and early. Present prototyping techniques, including 3D printing, can reduce material costs by allowing components, and/or the entire part, to be modeled in advance of building expensive tooling.
Injection Molding Design Guidelines
Essential Rules for Strong, Easy-to-Make Plastic Parts
Wall Thickness
- Keep thickness consistent throughout the part
- Most small parts: 2-3mm thick
- Make changes gradual, not sudden
- Prevents warping, sink marks, and stress
Corner Curves
- Inside corners: 0.5-0.75x wall thickness
- Outside corners: 1.5x wall thickness
- Eliminates stress concentration points
- Improves plastic flow and mold release
Material Selection
- Consider strength requirements
- Account for shrinkage characteristics
- Evaluate environmental exposure
- Affects wall thickness and draft needs
Ejection & Parting Line
- Plan early in design process
- Determines rib and hole placement
- Simplifies mold design
- Avoids visible seam lines
Ribs
- Thickness: 50-75% of wall thickness
- Height: Max 2.5-3x thickness
- Spacing: 2x thickness apart
- Draft: 0.5-1.5° per side
- Curved base: 0.25-0.5x thickness
Holes
- Distance from edges: 1+ diameter
- Blind holes depth: 2-4x width
- Through holes depth: 3-10x width
- Add bosses and ribs for strength
Draft Angles
- Minimum: 0.5° for smooth surfaces
- Standard: 1-2° for most applications
- Textured surfaces: 3-5°
- Add 1° per inch of depth
Quick Design Rules
Essential checkpoints for successful injection molding
Maintain uniform wall thickness with gradual transitions
Curved corners improve plastic flow and reduce stress
Use ribs for strength without adding bulk
Reinforce holes with bosses and connecting ribs
Draft angles ensure easy part ejection
Design ejection strategy from the beginning
injection molding troubleshooting
PROBLEM | REASON |
---|---|
1. Short shot | The plastic parts made by plastic injection molding companies have irregular and incomplete edges. It usually occurs at the farthest point of the gate, the roots of thin and long ribs. |
2, Shrinkage | Occasionally, a place 1. when the material thickness is uneven, 2. thick section of injection molded part, 3. boss and rib section. Due to shrinkage, the plastic parts develop dent, uneven, and wavy under low light |
3, Flash | A part edge with an extra thin layer of plastic is often found in the following locations 1. Parting line; 2. Moving core; 3. Ejector pin position, boss position, hole position, snap location |
4. Bubbles | The bubbles on the plastic surface are of a different color from the surrounding colors and are typical 1. bubbles caused by gas, air, and water-gas that are not released in time. 2. bubbles caused by shrinkage. The bubbles in the transparent part are particularly distinct. |
5. Weld line | When multiple molten flow fronts coincide with each other, a deep weld mark appears on the surface of a plastic part. This most commonly occurs at the confluence of multiple molten flow fronts. |
6, Burning | it is not a flat surface. It is usually dark or black spots; usually, they are found in sections where it is difficult to fill and trap the gas easily. |
7, Black spots | black impurities are evident on the surface of the plastic parts, mainly caused by the use of mixed materials. |
8. Discoloration | The slight difference in color between the actual plastic part and its required color is very apparent, and it is generally because the pigment is incorrect, the mix ratio is incorrect, or the mold is set at the wrong temperature. |
9. Wrinkles | The plastic parts show wavy lines on the surface caused by the cooling of the resin flowing. |
10. Deformation | The plastic parts have distortions, undulations, curves, and this is particularly common in the bosses, ribs, and round-shaped injection parts. These are especially common to PP injection molding. |
11. Wrong materials | In contrast to the specified materials, the one here can be identified by checking out the packaging label, the density, the burning continuity, the color of the flame, the color of the smoke, and the length of flames. |
12. Stick to the mold | Incomplete plastic part staying in the cavity, in contrast to short-shot, or due to the lack of designing the mold ejector system, the plastic part is hard to be ejected from the cavity, generally in thin-walled areas, bosses, and snaps. |
13. Scratch | The surface of the plastic parts rub against the surface of the cavity during the ejection so that a lot of them have scratches on the surface. |
14, Over-flow | It is caused generally by cavity damage and occurs on the active section, bosses, ejector pins, and parting surface. |
pros and cons of Plastic Injection Molding
We all know that plastics play an integral role in everyday life (and yes, even though we say it, we do advocate a sustainable and effective use of plastics). Injection molding introduced a new way to produce plastics in this industry. Using this technique, a variety of plastic products can be produced in an easy and cost-efficient manner.
pros:
Exactness
The plastic molding process is accurate and can be used to manufacture almost any type of part. Using the process, it is possible to obtain any shapes with complex geometries, due to its efficiency and its practicality. This process also allows for the production of parts with complex geometries. In addition, it can be used to produce large quantities of items, which makes it suitable for mass production.
Quick process
Injection molding is more convenient and faster than traditional molding techniques. It takes 15 to 20 seconds for the cycle of production to complete. Injection molding materials differ in their structure, which affects the speed of work.Injection molding is a continuous process, which allows for the manufacture of large quantities of products in a short time. This is especially useful when dealing with high-demand products.
Cost-effectiveness
Injection molding is usually automatic, so it minimizes supervisory costs. It also keeps production moving forward while maximizing efficiency.Rather than hiring multiple people for different tasks, you could train one of your employees to use the machine.
The injection molding process is inexpensive compared to other types of processes that use metal molds or dies. This makes it ideal for small businesses and startups who want to save on costs while still producing high-quality products.
Sustainability
From an environmental perspective, it is vital that injection molding manufacturers weigh the positives and negatives of their production. In addition to being practical, plastic moulding is also a sustainable method of reducing environmental impacts. Unlike a new product, injection molding uses a limited amount of resources and focuses more on recycling.
Versatility
Over the last couple of years, injection molding techniques have become a lot more sophisticated. Technological and machine options are plentiful. The good thing about injection molding is that it is common throughout the world, so if something goes wrong, it is easy to fix.
Injection molding is a very versatile process. It can be used to make almost anything that you can think of—from small plastic parts for electronic devices to large components for cars and trucks. The only limitations are those of the injection molding machine itself and the material being molded. Machines come in all shapes and sizes, from tabletop models that can produce products as small as a cellphone case, up to huge industrial machines capable of making everything from car seats to airplane wings.
cons:
There is a normal perception that injection molding method is the only suitable and price efficient method for the production of plastic components for mass production. In reality, plastic molding does have many drawbacks that should be seriously considered before making any final decision.
Tooling and press Costs
Injection molding is an expensive process for setup. You have to pay for the injection molding machine, as well as the raw material costs.
Tooling costs are one of the largest expenses in injection molded products. The cost of making molds can be very expensive due to their complexity and the high quality required for them. In addition to tooling costs, there are also maintenance costs which include repairing or replacing broken tools or worn out molds which can be quite costly.
time consuming
Injection molding is a time-consuming process. Not only does it take weeks or months to design your injection molds, but the actual injection molding process itself can take anywhere from three to seven days.
skilled labor
One of the most important elements in producing a quality plastic product is precision and accuracy. To ensure these qualities, it requires precision, accuracy and skilled labor to produce a quality product. In order to produce a high-quality injection molded product, businesses must take these factors into account and make sure that their plastic products have the desired results.
Manufacturing defects
Injection molding is one of the most accurate processes available, but it can also be inaccurate. This inaccuracy can lead to manufacturing defects, which can cost companies money and time. It is important for companies to be aware of these defects so they can correct them before they cause any damage.
hard to recycle and dispose
Injection molding is an unsustainable process that leads to waste and pollution. As a result, injection molders have a responsibility to ensure that their products are being recycled effectively. This can be difficult because it requires coordination between multiple parties: the company that makes the product, the company who sells it and consumers who use it once they purchase it. Many companies don’t take this responsibility seriously enough, which leads to plastic pollution across our planet.
It’s difficult to recycle injection molded parts due to their complex shapes and sizes that require specialized machinery to handle them properly. Also, because these parts are made from multiple materials (plastic, metal or rubber), they require different types of recycling processes — making them even more difficult to recycle effectively than other types of plastic waste materials such as bottles or bags.”
The 6 Different Types of Plastic Molding
There are several different types of plastic molding, each with its own unique characteristics and benefits. Here are six common types of plastic molding:
- Injection molding: This is a common method of producing large quantities of plastic parts. It involves injecting molten plastic into a mold cavity, where it cools and solidifies into the desired shape. Injection molding is fast and efficient, and it can produce highly precise and consistent parts.
- Blow molding: This process is used to produce hollow plastic parts, such as bottles and containers. It involves heating plastic until it is pliable, then using air pressure to blow it into a mold cavity. Blow molding is often used for large, complex parts with thin walls.
- Extrusion molding: In this process, plastic is melted and forced through a die to create a continuous shape, such as a pipe or a sheet. The resulting shape is then cut to the desired length. Extrusion molding is often used for products with a constant cross-section, such as pipes and tubes.
- Thermoforming: This process involves heating a sheet of plastic until it is pliable, then forming it over a mold using vacuum pressure. Thermoforming is used to produce a wide range of products, including cups, trays, and packaging materials.
- Rotational molding: In this process, a mold is filled with powdered plastic and then rotated in an oven to distribute the plastic evenly. The mold is then cooled, and the resulting part is removed. Rotational molding is often used for large, hollow parts with complex shapes.
- Compression molding: This process involves heating a plastic charge and pressing it into a mold cavity under high pressure. Compression molding is typically used for medium- to high-volume production of parts with simple shapes and uniform wall thicknesses.