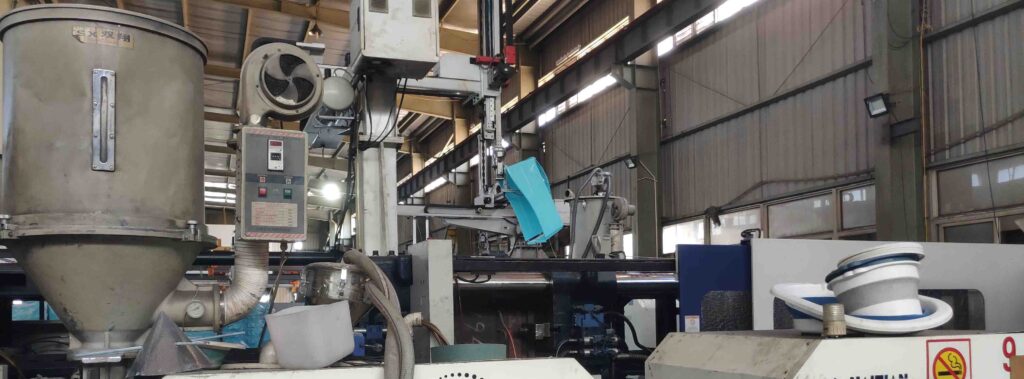
In the machine industry, there are many people who are aware that Plastic Injection Molding is just as necessary and important as any other machining process. Plastic injection molding equipment should be purchased after considering the following factors: shot volume, tie bar distance, ejector travel, platen dimensions, and tonnage.
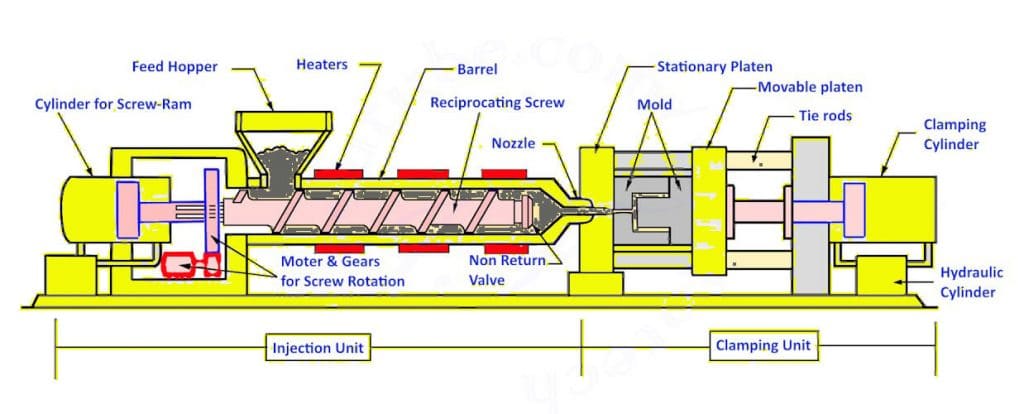
- Shot Volume
An injection molding machine’s shot size refers to how much plastic it can inject into a mold cavity during a single molding cycle. In the U.S., the amount of “general purpose polystyrene” (GPPS) is measured in ounces, while in Europe and Asia it is measured in cm3.
It is a good idea to always search for a machine that can produce 30-40% more shots than the size of your parts.
- Platen Dimensions
Platens are the tools that hold the cavity of the mold. Platens are inserted and clamped securely to the mold, which is spaced apart. During the molding process, the two platens are brought together and held under tonnage pressure. Following heat and injection, the plastic is cooled through a cooling cycle. Several tons of pressure are applied to hold the plastic in place as it takes on its final shape after hardening.
- Tie Bar Distance
Injection molding machines have horizontal tie-bars, termed “tie bar spacing,” between which the molds are installed. Accordingly, the holes in the platen allow molds to be ejected. These measurements determine the maximum size of molds that will fit in the molding machine, along with the platen maximum spacing.
- Ejector distance
With an ejector stroke, the machine pushes the workpieces from the plates with the assistance of ejector pins. During the molding process, the ejector is attached to ejector rods or pins on the mold which push the molded part out after the plastic has hardened.
- Tonnage
As far as clamp pressure is concerned, it could be viewed as the same as when you examine press brakes. For press brakes, the tonnage capacity is measured by the amount of downforce that can be directed towards the workpiece. The amount of force that injection molding machines can apply to the platens, which support the mold cavity, is measured in tons by how much plastic can be injected into the cavity.
Molding begins with the melt plastic flowing in the mold and working its way out of the cavity by extruding the ejector pins. When pin movement is timed with mold opening, it helps prevent pins that are moving too quickly from damaging the plastic workpiece or pins that are moving too slowly from not ejecting the molded part completely.