Develop new plastic parts requires taking an in-depth and systematic approach in order to guarantee successful design, manufacturing and implementation. From setting requirements through testing and quality control procedures – every stage plays an integral part. In this article we’ll go deeper into each stage of developing new plastic parts, providing insights and advice along the way.
Establish Clear Requirements and Objectives:
The initial step in developing plastic parts requires clearly outlining their requirements and objectives, including intended applications, functionality requirements, dimensions strength requirements desired properties environmental conditions regulatory compliance needs etc. By having an in-depth knowledge of all these elements a strong basis can be laid for design and manufacturing processes to follow.
Engaging stakeholders, including engineers, designers and end-users during the requirement definition phase is imperative in gathering input and insights that ensure your design meets with desired criteria and meets intended outcomes. By including appropriate experts who understand target audiences needs as part of this effort, you can ensure the desired design outcomes will be realized.
Conceptual Design:
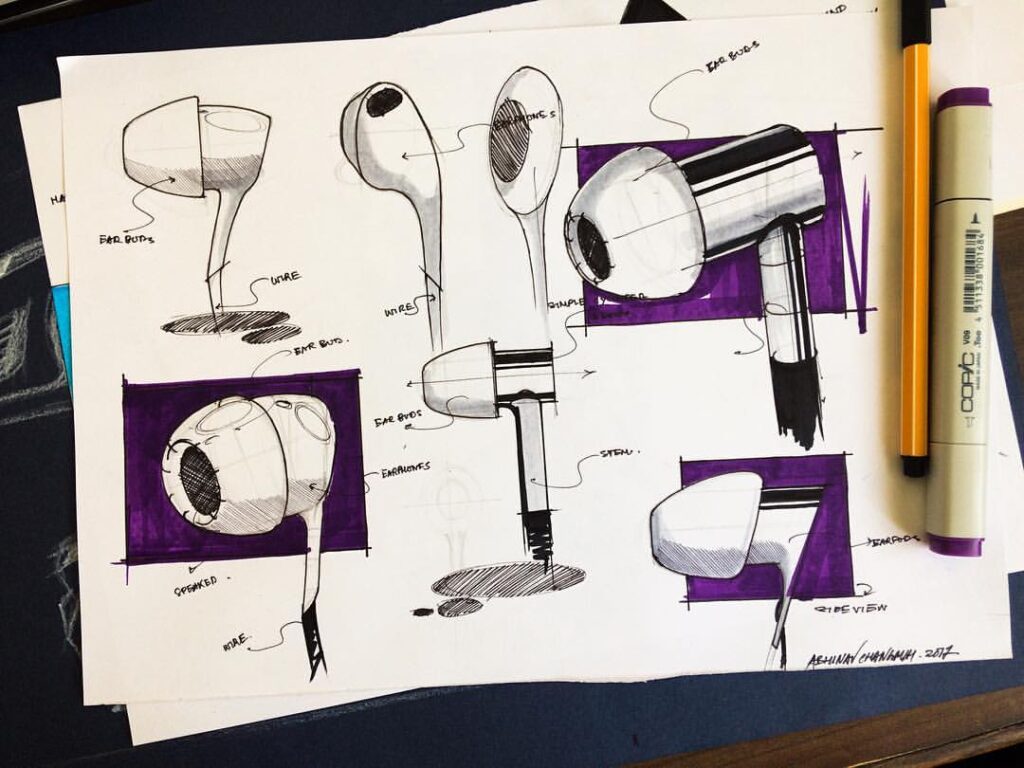
Based on your requirements, the next step should be designing the plastic part conceptually. This involves translating your requirements into visual forms using computer-aided design (CAD) software so designers can produce 3D models which demonstrate its shape, form, and assembly requirements.
Design software:
- SolidWorks,
- AutoCAD,
- Fusion 360
- Moldflow:
- Siemens NX:
- Solid Edge
- CATIA
As part of the conceptual design phase, it is crucial that designers iterate on their designs frequently with feedback and revisions in mind, to refine them further and meet all requirements adequately. Furthermore, early identification of any issues or obstacles related to manufacturing helps facilitate problem resolution more swiftly and cost effectively.
When it comes to file formats for plastic component design, the following formats are commonly used:
- CAD Formats:
- DWG (AutoCAD Drawing)
- DXF (Drawing Exchange Format)
- DGN (MicroStation Design)
- PRT (Part)
- 3D Model Exchange Formats:
- STL (Standard Tessellation Language)
- STEP (Standard for the Exchange of Product Data)
- IGES (Initial Graphics Exchange Specification)
Material Selection:
Selecting an ideal plastic material for any part development is of vital importance in its success. Deliberations over which plastic to select can depend upon several considerations such as desired mechanical properties, environmental implications and aesthetic demands as well as cost constraints. Common injection-moldable options are
- Polyethylene (PE)
- Polypropylene (PP)
- Polyvinyl Chloride (PVC)
- Polyethylene Terephthalate (PET)
- Polystyrene (PS)
- Acrylonitrile Butadiene Styrene (ABS)
- Polycarbonate (PC)
- Polyamide (PA)
- Polyethylene Terephthalate Glycol (PETG)
- Polyvinylidene Fluoride (PVDF)
- Polyurethane (PU)
- Polyoxymethylene (POM)
To select the ideal material, it is necessary to carefully evaluate each option’s properties and characteristics – including strength, durability, flexibility, temperature resistance, chemical resistance and cost – prioritising one option over others. Consulting material suppliers or experts for advice in choosing an appropriat material ensures it satisfies desired requirements.
Design Validation:
After concluding the conceptual design and material selection phase, it becomes essential to perform a meticulous design validation process aimed at verifying if the intended functionalities are met before advancing with production. Validation can be done through simulation software or physical testing or both depending on product complexity needs.
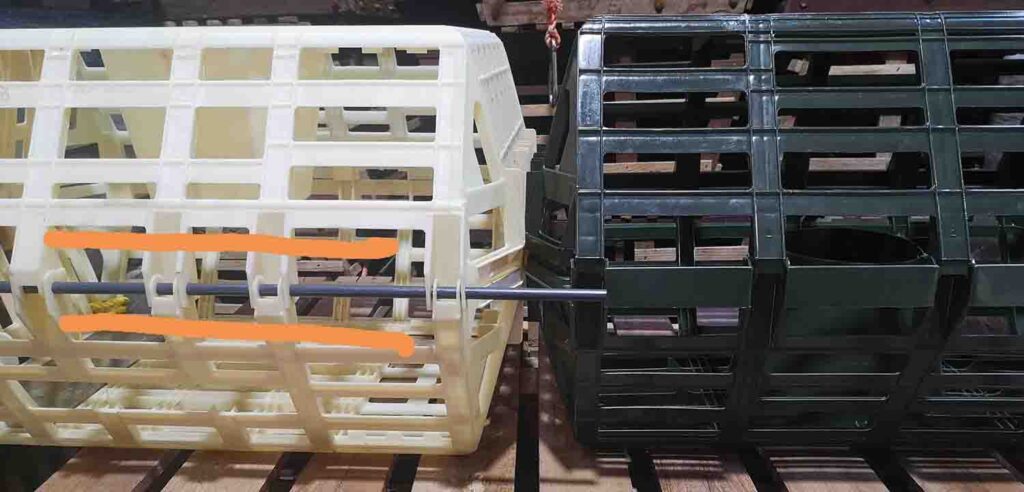
Simulation software enables evaluations across numerous domains encompassing stress distribution, moldability among other technicalities giving clear insights into feasibility & optimization solutions through measuring various scenarios& load capacity factors at an early stage before production hence avoiding failure risks that may arise later in the development process.
Physical tests aid in validating parts performance against specific criteria such as dimensional accuracy measures via environmental stability factor checks , tensile scans or impact resistance levels needing confirmation for each part’s unique needs; these tests further ensure conformance with required regulations & customer satisfaction levels.
Tooling and Manufacturing:
Once a design has been verified, the next step in manufacturing involves creating the appropriate tooling – typically designing and fabricating injection molds suited for this particular part. Injection molds play an integral part in this process as they define its final form and shape.
Collaboration with an experienced tooling manufacturer is integral for producing an accurate mold. Designers and tooling experts will assist with this process during tooling production.
Together we will collaborate closely on designing molds with optimal design, selecting materials to use in them and installing appropriate cooling and ejection systems. Working closely together will also include engaging an experienced tooling manufacturer as a consultant on all matters regarding mould design, material selection and manufacturing considerations to streamline production process and maximize productivity.
Mold flow analysis (a simulation of injection molding process), conducted during tooling phase can detect issues like air traps, weld lines or excessive shrinkage that need addressing in order to increase overall quality and consistency in final plastic parts produced from injection molds. By taking action at tooling stage instead of later down the production line, quality and consistency in final plastic parts produced can be drastically increased.
Injection Molding:
Injection molding is one of the most efficient means of producing plastic parts, using high pressure injection to force liquid plastic into mold cavities and let it solidify as it cools off and solidifies over time. However, to achieve maximum effectiveness this requires precise control over several parameters like temperature and pressure before cooling time is reached – all which must be monitored closely for optimal results.
Partnership with an experienced injection molding vendor is paramount for proper setup, process optimization and quality control during production. They’ll collaborate closely with design teams in selecting materials suited for optimal injection molding parameters based on material properties and part specifications.
At each stage of injection molding production, quality control measures must be implemented in order to monitor production and ensure that manufactured parts meet required standards and specifications. These may include dimensional inspections, material property tests and functional tests which verify part performance and quality. By employing robust quality assurance processes any deviations or issues can be identified quickly thereby minimizing waste while assuring consistent part quality.
Testing and Quality Control:
The development of new plastic parts requires careful implementation of testing and quality control procedures for optimal results. It is critical to validate their performance with robust testing methods that examine their durability, reliability and mechanical properties. Dimensional inspections assure compliance with defined specifications in addition to material property assessments such as tensile strength impact resistance or thermal stability analyses for enhanced understanding of these qualities.
Functional aspects of the plastic parts are equally important as they reflect usable performance while being assembled or fitted together properly according to design specifications which SPC helps maintain throughout production cycles by continuously gathering data from its scope applying established methodologies while doing so.
Lastly but no less important is careful consideration directed towards long-term performance; achieved only through consistent adherence towards effectively recalibrating materials chosen after conducting accelerated aging tests environmental stressors such as exposure whether from elements outdoors etc provide insights into expected lifespan metrics ultimately aimed at delivering greater consumer value.
Implementation and Feedback:
Once new plastic parts have been developed and tested successfully, their next step should be integration into an application or product. You should monitor performance while gathering feedback from users or clients so as to gauge satisfaction levels as well as identify any improvements or modifications required.
Continuous Improvement is a cornerstone of development. Regularly review and modify design and manufacturing processes based on feedback or lessons learned to continuously enhance efficiency, reliability, and performance in plastic parts.
Conclusion:
Generating new plastic parts requires an organized and comprehensive process involving numerous stages from requirements definition through testing and quality control. By working with experienced professionals and
following these steps you can successfully design new plastic parts that fulfill their intended applications, offering functionality, durability, and reliability in their applications. Engage stakeholders when possible for effective involvement as you validate designs, select suitable materials for manufacturing processes that optimize productivity as well as implement robust quality assurance measures so as to produce high-quality parts which contribute significantly towards project success.