PET preform mould, preform mould maker in China
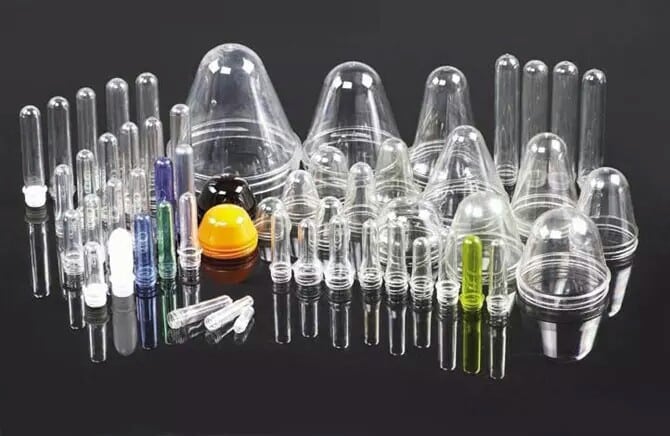
How to Buy PET Preform Mould: Precision Solutions for Bottle Manufacturing
To buy high-precision PET preform moulds select suppliers based on their expertise and material durability and industry standards compliance. A good mould design maintains rapid cycle times and stable output quality.
3-Step Guide to Procuring PET Preform Moulds
Start by defining your requirements for capacity and cavity count while requesting CAD drawings from certified suppliers at [Product Name].
Check for ISO 9001 and FDA certifications while examining test results which demonstrate bottle PET preform moulds have a maximum tolerance of 0.01mm.
The warranty coverage must include wear-resistant steel components which have shown 1M+ cycle durability in research studies.
PET Preform Mould vs. Competitors
Factor | Generic Moulds | [Product Name] |
---|---|---|
Material Quality | Prone to corrosion (6M lifespan) | Chromium-coated steel (15M+ cycles) |
Production Speed | 18-22s cycle time | 12s cycle time (tested) |
Customization | Limited cavity options | 96-cavity designs available |
The Most Common Uses of PET Preform Moulds Include
• High-volume beverage bottle production (Why choose PET preform moulds over blow moulding?)
• Custom medical/pharma packaging with FDA-grade materials
• The production of eco-friendly lightweight containers happens through the use of recycled PET materials that reach 30% content.
The bottle PET moulds from Topworks use 19% less energy during production than standard industry practices show. Select moulds with valve hotrunner systems since these systems deliver maximum ROI and match your production requirements.
TopWorks has operated as the leading supplier of dependable PET preform moulds at affordable prices for more than ten years. Our team applies modern technology to high-quality steel materials(S136,H13) and creates durable cost-efficient molds which have earned us local and international customer trust through our dedication to customer satisfaction.
The ongoing optimization and innovation work of our staff aims to produce exceptional quality outcomes from our production process. Our PET preform moulds benefit from more than ten years of experience at TopWorks ,which guarantees that we will deliver products which satisfy our customer requirements. TopWorks stands ready to become your ideal supplier for premium preform molds that come with affordable pricing.
“I’m glad to inform you that all plastic parts are perfect!!! We are delighted, and therefore there are good chances to continue our relationship for any coming new project.”
CRISTIANO
ITALY
“Steven is a very detail-oriented project manager and engineer who can solve problems creatively and also provides excellent service. It was a pleasure working with him.”
DAVID
USA
Overview of company’s PET preform mould making
PET Preform Mold Design
- Technical design considerations
- Mold configuration (cavities, layout)
- Gate design
- Cooling system
- Ejection system
- Venting
- Surface finish
- Tolerances
PET Preform Mold Materials
- Tool steel options
- P20
- H13
- 420 stainless steel
- Other alloys
PET Preform Mold Making Process
- Steps involved
- Mold design
- CNC machining
- Heat treatment
- Finishing
- Assembly
- Testing and approval
Our team
The specialized workforce at Topworks builds and designs moulds for making unique features that match various types of PET plastic preforms. We have complete capabilities to create plastic preform molds throughout our pleasant manufacturing environment.
The production facility provides preforms for purchase which can be produced for individual packaging requirements by creating customized PET preform moulds. Customers can acquire all necessary items through this complete solution that operates from a single location.
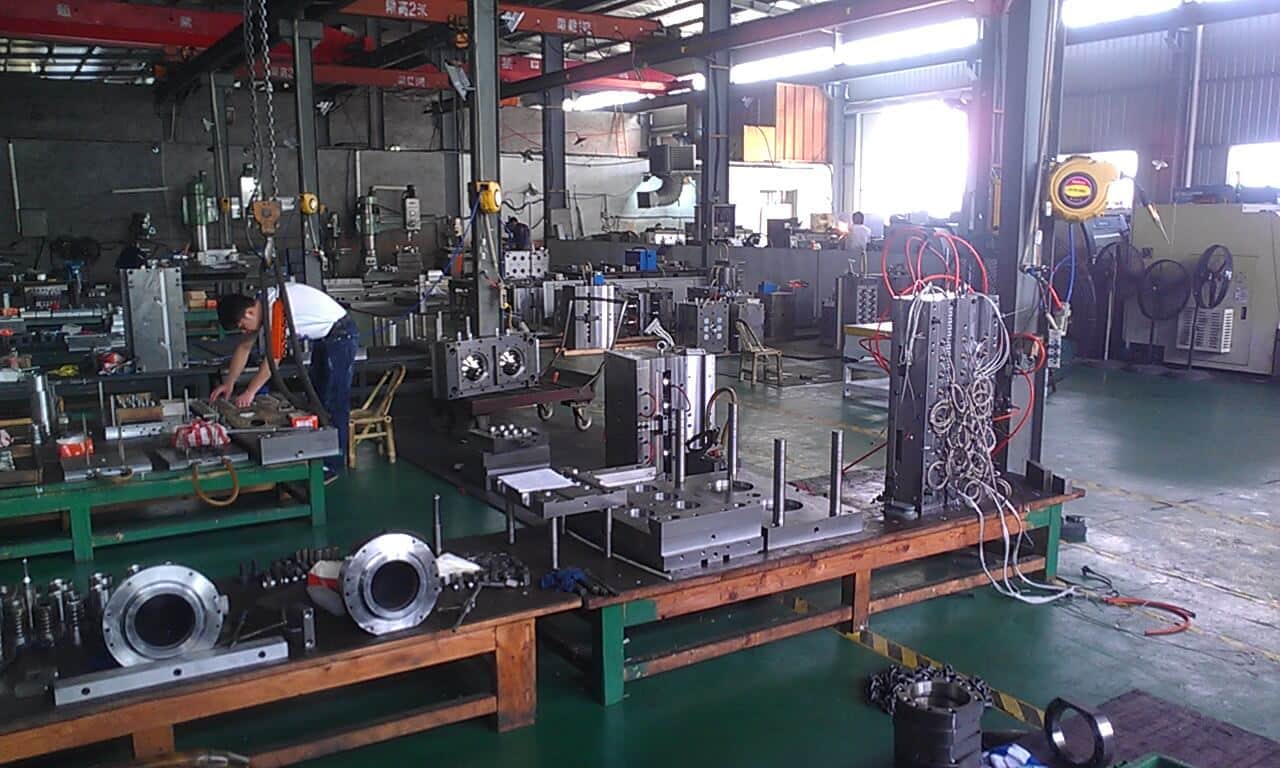
How to use PET preform mould?
Polyethylene terephthalate (PET) stands as a naturally occurring thermoplastic polymer which industries widely use in plastic products. GF-PET serves as the most widely chosen polymer for customer applications while preform injection remains its primary usage. A liquid PET material exhibits superior properties and pressure plays a more vital role than temperature in determining viscosity. The fluidity of the melt depends mostly on pressure during this situation.
Plastic Processing
PET pellets demonstrate high sensitivity to water during heating because of their both hydrophilic and lipid-based nature. The structural composition of PET includes phospholipids because of their presence. The substance changes to a brittle state alongside color changes when water concentration surpasses the established limit and causes PET to lose its molecular weight.
Processing requires a temperature of 150 °C for a minimum period of four hours while the typical range stays between 170 °C and three to four hours before production starts.
The quantity of recyclable materials must remain lower than 25% while any use materials need a complete drying process prior to application.
Injection Molding Machine
The injection system needs temperature control elements and low-friction heating because PET maintains its shape after melting and has a high melting point while the plastic weight should match 2/3 of conventional one-shot machine dosing.
Mold and Gate Design
Hot runner molds function as the equipment for producing PET preforms. The injection molding machine needs a heat insulating material to exist between itself and the hot runner mold. The thickness of preforms reaches 12 mm and insulators need to handle elevated pressure levels.
Excessive depth of 0.03mm in the venting slot will cause flash to appear.
Melting Temperature
By utilizing the shot-to-air method the suitable temperature range extends from 270 to 295 ° C. The best temperature range for enhanced grade GF-PET stands between 290-315 degrees Celsius.
Injection Speed
Material coagulation can be prevented when the injection process takes 2 to 4 seconds. High speed injection causes material brittleness. The shot takes four seconds.
Back Pressure
The injection pressure should remain under 100bar since this level offers the best performance for maintaining the process.
Residence times
Molecular degradation will be prevented when keeping temperatures lower than 300 °C and residence times shorter than 15 minutes. The cleaning process through air-blasting the barrel should not exceed 15 minutes of operation time but if further cleaning is required use viscosity PE while lowering the barrel temperature to PE temperature.
Others
The excessive use of recycled materials should be avoided since it could affect plasticization in a negative way. White fog together with opaque appearance can emerge from uncontrolled mold temperatures.
Why valave hotrunner system for PET preform mould
The initial price and delivery are often driving factors in today’s injection molded preform. As a result of this sort of PET mold acquisition, molded parts will not be at their long-term economic advantage for companies producing the first generation of parts. At the same time, even short-run molds will not contribute fairly to the bottom line profits. Tooling is often modified when molders make a new generation of the same basic part, believing that by doing so, the pPET preform production will be so successful that the competition will not win the contract. An opponent with long-term parts production molds, which have the best ROI compared to a production run, will be in a stronger position in rebidding, especially if the same procedures reflect the entire company’s outlook.
When selecting a system, consider these factors
Injection molded PET preform, whether short-run or long-run, need to be evaluated from the points below. All aspects of an economically successful PET preform mould operation must be considered when selecting a gating system: its cost, trial costs, setup times, cycle times, maintenance, scrap, secondary operations, auxiliary equipment, and the quality of its parts. Mold size is enhanced by the runner and offset of the cavity from the sprue bushing in a cold bushing, single cavity mold with edge-gating of the part. With well-designed systems, the resin will be moved to the offset with the minimum increase in PET preform mould size via a low-profile hot runner.
Hot runner costs are offset by reduced PET preform mould size
Even if the PET preform mould size is reduced, the hot runner’s initial cost may be offset, allowing the press size to be chosen based on part requirements. The valve gate to the parting line reduces the amount of resin required per shot, thus reducing scrap (sprues) and regrind volume required. It makes economic sense to use a hot runner to replace mold offset for all parts over 50g with an expected life of more than 150,000 pieces. Due to the expensive mold base for a cold runner system, the number of parts may be lower when the part is larger, but the cost of hot runners will stay the same.
PET preform mould sprue bushing advantages
Molds that gate directly into a single cavity using a sprue bushing have several advantages over cold runners. Based only on the part requirements, the PET mould base size will be determined by the smallest press. By using cold sprue bushings, sprues are created, which must be removed, leaving marks that frequently need to be removed through secondary operations if appearance or maximum height of the sprue remnant are concerns. Hot sprue bushings are commonly used to prevent this, but often leave an unacceptable mark, reduce the operating window, and create internal part stress (warpage).
By using a valve gate system, an unacceptable mark will not form, a good operating window is maintained, and the PET preform is provided with the least amount of stress. Valve gate systems typically require a larger mold for their operating system, both in terms of mold footprint and height, because they must use a hot runner to offset the operating mechanism from the centerline of the mold, and have to fit a manifold and their operating mechanism in the mold. Most suitable systems will achieve this without increasing the footprint of the PET mold, and often without affecting the height of the mold, since the valve gate is situated on the centerline of the mold and does not require external operation.
Bigger PET preform mould as a Result of Cold Runner
The size of the preform mould is often increased when designing multicavity moulds with cold runner systems in order to fit the runner, slides, and mechanisms, which in turn makes it more difficult to orient the cavity during complex part design. If part modification or long process times are involved, the molding process operating window becomes very restricted and warpage is almost impossible to control.
In the manufacture of three-plate molds, cavitation levels are high, cavity layout is optimal, and automatic operation is possible. The incorporation of a hot runner system with direct thermal gating in place of traditional mold construction will allow the multicavity mold to be utilized in a more economical manner–smallest parting line surface per part, low mold height, shorter cycle times, least scrap, and best automated operation.
In addition to reducing cycle times, valve gated hot runners reduce part stress and produce better quality preform parts. In contrast, new valve gated hot runner systems, which increase mold height no matter what and are less expensive, can greatly reduce the costs and mold height increases of traditional valve gated hot runner systems that have a detrimental effect on economic efficiency. Hot runners may be ordered for the entire “A” half minus cavities in order to assure better mold delivery times. Mold construction time can be reduced by spreading the workload across more facilities.
PET preform mould Hot Runner System Offers Cost, Time, and Waste Reduction
A hot runner system has been applied to the acquisition of preform mould and has proven to be an efficient way of reducing the initial cost, construction time, and operational costs of trials, setup, cycle time, maintenance, scrap, and secondary operations-and without requiring any additional equipment. As a result, most applications will be able to expect a consistent level of quality. A hot runner thermal gated system or a valve gate system is frequently specified to produce a high-performance molding design. Using these types of machines, you will achieve very high shot-to-shot repeatability, faster cycle times, easy mold operation, and high-quality parts. Thermal as well as valve gate systems designed well will generally outperform those designed poorly. With such a system, less mold height and less power is needed, plus no external controls or auxiliary power systems are required.
Almost any PET preform mould acquisition should consider a hot runner system due to the advantages it will provide overall. To obtain the advantages necessary for competitive injection molded parts production in today’s market, valve gate installations should be performed as per the manufacturer’s specifications. Valve gate systems are superior to thermal gate systems because all components are constructed very simply and robustly, from a simple design concept of as few parts as possible to provide the best gate flow control.