Why venting important?
In a sense, the injection mold is also a displacement device where the hot plastic melt enters the mold cavity while displacing the air in the mold cavity.
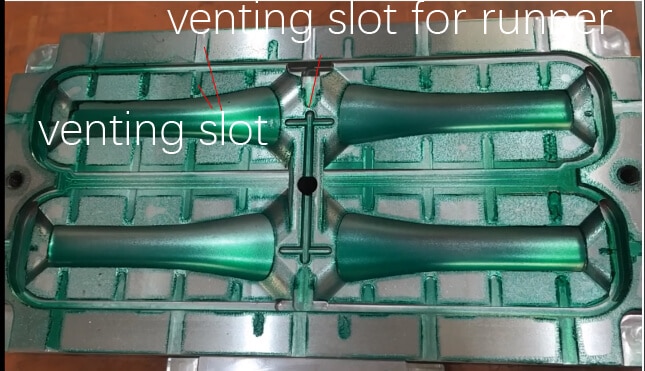
In fact, the air in the mold is not limited to the cavity, especially the three-plate injection mold, and the air existing in the flow path cannot be ignored.
In addition, the plastic melt produces a small amount of decomposition gas. These gases must be discharged in time.
If the venting performance of the mold is poor, it is easy to produce bubbles, silver streaks, clouds spot, short shot, scorch marks and other defects.
Therefore, a reasonable layout of the venting structure should be provided on the mold to avoid defective products caused by poor venting.
Venting slot
For the molds for making large and medium-sized plastic parts, the amount of gas removed is large. Generally, the Venting slot should be cut on the side of the plastic mold on the parting surface.
The position of the venting groove is preferably at the end of the melt flow, and the size of the venting groove design is based on the principle that the gas can be smoothly discharged without overflowing. The width of the exhaust groove is generally about 3-5mm, the depth of the front end of the exhaust groove is less than 0.05mm, and the length is generally 0.7-1.0mm.
Plastic Material | Slot Depth (mm) | Plastic Material | Slot Depth (mm) |
---|---|---|---|
PE | 0.02 | ABS | 0.03 |
PA (GF) | 0.03-0.04 | PC | 0.04 |
PP | 0.02 | SAN | 0.03 |
PA | 0.02 | PBT (GF) | 0.03-0.04 |
PS | 0.02 | ASA | 0.03 |
PC (GF) | 0.05-0.07 | PBT | 0.02 |
- Part line venting
The parting surface gap can be used for venting for small molds, but the parting surface must be located at the end of the melt flow.
- insert venting
For a combined core or cavity, it can be vented via an inserted gap.
- ejector pin venting
Use the fit of the ejector pin to the plate or the core to vent, or intentionally add the gap between the ejector rod and the mold plate.
- Powder unsintered alloy venting
The powder sintered alloy is a material sintered by a spherical granular alloy and has poor strength, but the texture is loose, allowing gas to pass. Place such an alloy in part to be vented to meet the exhaust requirements, but the diameter of the bottom vent should not be too large to prevent the cavity pressure from squeezing and deforming.
- slug well venting
On the outside of the junction of the plastic melts, a well is provided to allow the gas to be discharged therein, and a good venting effect can also be obtained.
- Mandatory exhaust
In the part of the closed section, the venting pin is arranged. This method has good venting but leaves a trace on the plastic part, so it should place the exhaust pin in the concealed part of the plastic part.
Things to be aware of when designing venting:
- When the venting is extremely difficult, the insert structure is adopted. If the dead angle of some molds is not easy to design the exhaust groove, the mold design should be appropriately changed into the insert without affecting the appearance and precision of the product. Good venting can also improve the machining processing and ease of maintenance.
- At the closed section of the plastic product, the ejector pin must be added for venting to prevent burn marks.
- For plastic molds with complex geometries, it is best to determine venting grooves after several trials.
- The thinner the plastic product wall is, the far away from the gate the section is, the opening of the venting groove is particularly important.
- For small plastic parts or precision parts, please pay attention to the design of the venting groove because it can avoid the defects of the product surface and the injection defects.
Summary:
The appropriate venting groove can greatly reduce the injection pressure, injection time, holding time, and clamping pressure, making the plastic injection parts difficult to easy, thereby improving production efficiency, reducing production costs, and reducing the energy consumption machine.