Scaling Injection Molding Costs with Production Volume
Injection molding is a very efficient process when you are making large quantities of plastic parts. Understanding how the costs of injection molding scale with volume is key to making good decisions on manufacturing strategy. In this article we will look at the relationship between volume and cost in injection molding and the key factors that influence it.
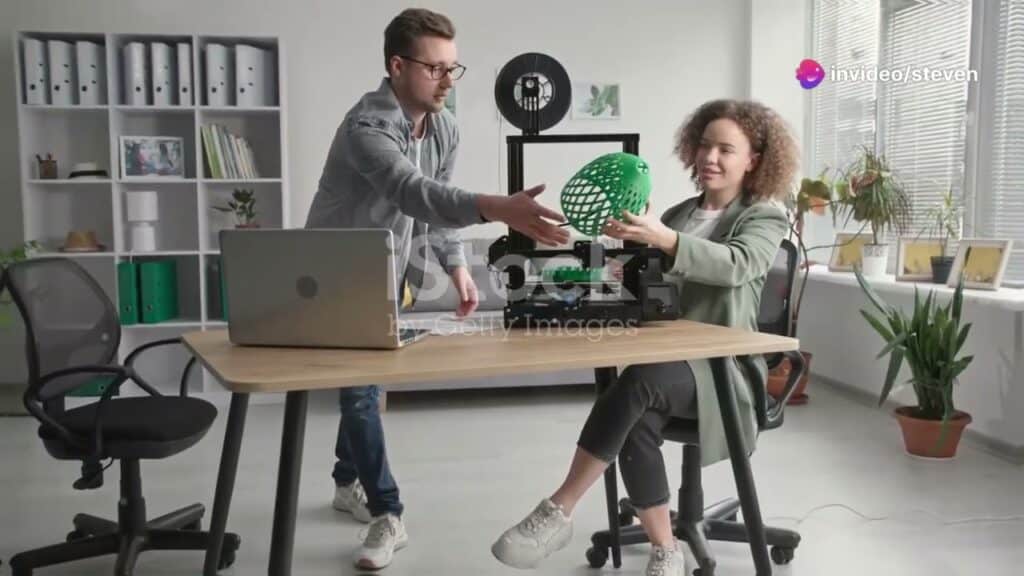
1. Initial Investment: The Cost of Mold Creation
1.1 Design Complexity
Detail: The complexity of the design comes with the amount of time and work required. More complex molds require more advanced engineering which can involve:
- Multi-Cavity Designs: Molds that produce multiple parts in a single cycle can be more expensive due to the complexity. For example a single cavity mold for a simple part might cost $5,000, while a 6 cavity mold for the same part could cost $20,000 or more depending on the number of cavities and design complexity.
- Undercuts and Features: Molds with undercuts or threads require sliders, lifters or unscrewing function which can add a lot to material and machining cost. An undercut mold might add 10-20% to the cost of a standard mold without undercuts.
1.2 Material of the Mold
Detail: The material of the mold is another factor that affects cost. Common materials are:
LKM | AISI | JIS | W.Nr | ASSBA | HB | HRC |
---|---|---|---|---|---|---|
P20M | P20Modified | – | 1.2311 Modified | 260-350 | 26-38 | |
2311 | P20 | – | 1.2311 | 280-325 | 29-34 | |
738 | P20Modified | 1.2738 | 290-330 | 30-35 | ||
738H | – | – | – | 330-370 | 35-40 | |
738 MH ESR | P20Modified ESR | – | 1.2738 Modified ESR | 718H | 341-400 | 36-43 |
838HS | P20Modified | – | 1.2738 Modified | 330-380 | 35-42 | |
808 ESR | P21Modified ESR | – | – | 360-415 | 38-44 | |
2083 | 420 | SUS420J2 | 1.2083 | S136 | 240 (max) | |
2083H | – | – | – | – | 280-320 | 29-34 |
2083 ESR | 420Modified ESR | SUS420J2 Modified ESR | 1.2083 Modified ESR | S136 SUP | 250 (max) | |
2316 | – | – | 1.2316 | 250 (max) | ||
2316H | – | – | – | – | 265-340 | 27-36 |
- Steel: Steel molds are durable and long lasting and are suitable for high volume production. But they are more expensive; a steel mold can cost from $5,000 to $100,000 depending on complexity and size.
- Aluminum: Aluminum molds are less expensive and quicker to produce and are good for low to medium volume production. Prices for aluminum molds are from $2,000 to $20,000. But they will wear out faster than steel molds so will need to be replaced sooner.
1.3 Lead Time
Detail: The lead time for the mold can also impact cost. A standard mold can take 4 to 12 weeks to produce. But if a project requires faster turnaround, manufacturers may need to expedite the process and add extra cost. For example:
Standard Lead Time: $2,000 for a standard mold.
Rush Order: A rush fee might add 10-20% to the cost so the same mold could cost $3,000 to $4,500 if expedited.
2. Scaling Impact on Mold Costs
2.1 Fixed Costs vs. Production Volume
The initial cost of the mold is fixed and does not change with volume. But as volume increases the impact of this fixed cost per unit decreases.
- Illustration:
- Example: Consider a mold that costs $20,000. If 10,000 parts are produced the cost of the mold alone is $2.00. If the volume increases to 100,000 parts the cost per unit is $0.20 showing the scaling effect.
2.2 Cost Distribution
As volume increases the fixed mold cost is distributed over more units which will reduce the per unit cost. That’s why injection molding is very cost effective for large volume production..Example:
Production Scenarios:
Units Produced | Mold Cost | Cost per Unit |
---|---|---|
10,000 | $20,000 | $20,000 / 10,000 = $2.00 |
50,000 | $20,000 | $20,000 / 50,000 = $0.40 |
100,000 | $20,000 | $20,000 / 100,000 = $0.20 |
2. Variable Costs: Material and Production Expenses
While the mold cost is fixed the other costs in injection molding are variable and scale with volume. These are:
2.1 Material Costs
- Raw Material: The cost of plastic material is usually calculated per pound or per kilogram. Larger volume production means larger material purchase and more bargaining power for large purchase.
- Scaling Impact: As volume increases the total material cost goes up but the cost per unit often goes down due to bargaining power.
2.2 Labor and Overhead Costs
- Labor: While labor cost can be somewhat fixed (machine operation and setup), it can also scale with volume. More parts produced might require additional shifts or overtime especially for high volume runs.
- Overhead: General overhead costs such as electricity, maintenance and facility costs are constant but the impact on per unit cost decreases as more units are produced.
Scaling Impact: Labor and overhead cost per unit goes down as volume increases so overall cost for larger runs go down.
3. Production Efficiency and Cycle Times
The speed of the injection molding process is another key factor in scaling cost:
3.1 Cycle Time
- Cycle Time: This is the time it takes to complete one injection molding cycle including injection, cooling and ejection. Faster cycle time means overall production efficiency and more units can be produced in a given time frame.
Scaling Impact: As volume increases the process becomes more efficient due to optimized machine settings and established workflows and reduces per unit cost.
3.2 Maintenance and Downtime
- Machine Maintenance: Maintenance is key to keep production running. As machines run more often over time they may require more maintenance which can lead to downtime.
Scaling Impact: While more volume can wear out the machine more, well maintained machines have less downtime and more consistent production and cost savings.
4. Cost Per Unit Analysis
As volume increases the cost per unit of injection molded parts goes down. Here’s how:
4.1 Fixed vs. Variable Costs
- Fixed Costs: Mold cost and overhead is constant regardless of the number of units produced.
- Variable Costs: Material and labor cost increases with volume but at a decreasing rate due to efficiency gained in production.
4.2 Break-Even
- Break-Even Analysis: Break-Even is where total cost equals total revenue. This is important for manufacturers to determine the minimum volume to justify the initial investment in molds and setup.
5. Summary
In summary the cost of injection molding scales with volume. The initial investment in mold is big but the cost per unit goes down as volume increases due to spreading of fixed cost over more parts and efficiency gained in material use and production process. For businesses that produce plastic parts understanding this cost structure is key to making decisions on production runs, budgeting and pricing. As a rule of thumb the higher the volume the lower the cost per unit and injection molding is the best for high volume production.