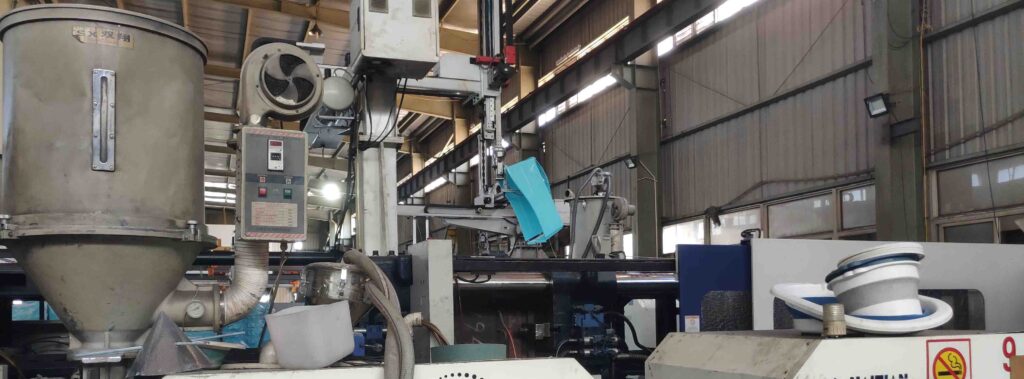
China Injection Molding Near Me and You -30% Cost Cut
Injection molding is one of the key business areas of Topworks Plastic Molding, one of the top China injection molding companies,and its injection molding department primarily focuses on injection molding near me and you and secondary operations.
It aims to enhance China’s injection molding product quality, improve production efficiency, control manufacturing costs, and make this complex process near you and me.
The company possesses the latest mold maintenance technology, nitrogen molding technology, and automated high-end production technology.
The company installs 30 injection molding machines from Toshiba and Haiti, with tonnage ranging from 40T to 1300T, to ensure the quality of products and boost production capacity.
- Various types of injection molding machines are available to meet the requirements of different customers.
- Our team has years of experience in the injection molding industry, and we are good at it. We specialize in all kinds of electronic appliances, and also household appliances and industrial products.
- We have been involved in various types of plastic engineering, including horizontal injection molding, vertical injection molding, and overmolding;
- The standard operation ensures the stability of product quality;
- Continuously improve production efficiency;
- Understand the different needs of customers, and provide them with high-quality China plastic injection Molding products that exceed their expectations.
Secondary Operation:
- Spray: PU paint, rubber paint, UV paint, high gloss paint, leather, metal paint, etc..;
- Printing: screen printing;
- Laser carving, plating, heat transfer, silk transfer;
- Hot melt, ultrasonic welding.
The plastic material :
- ABS(with glass fill)
- Polystyrene
- Polypropylene(with glass fill)
- Acrylic
- Acetal
- Nylon(with glass fill)
- PBT(with glass fill)
- PC(with glass fill)
- PC/ABS
What information is needed for China plastic injection molding companies ?
The following are the items included in the calculation of actual injection molding manufacturing costs. Injection molding is deemed a primary manufacturing process.
- Raw material
- Recycled substance
- Labour, direct and indirect
- Timed versus non-timed
- Rate (hourly) for machine
- Setup fees
- Downtime allowances
- Mold cavity count
What behind the price for Chinese injection molding ?
The plastic part price from China plastic injection molding companies depends on raw materials, labor, packaging, and set-up costs.
It’s not difficult to determine the cost of these factors because they are known and can be calculated before the project begins.
However, two factors make pricing a plastic part difficult, and that causes the greatest difference in pricing between competitors.
They are exact press cycle time and exact part weight.
These two factors are difficult to calculate because they are unknowns.
A company will only have to estimate cycle time and part weight until a sample part is made.
Plastic injection molding companies estimate the part price by using the experiences they have had making similar parts. After the sample part is made, a company can give an accurate price for the part.
For example, let’s go through an example using a blueprint or part drawing; the engineer will calculate the part volume. Then, using the specific gravity of the specified plastic, they will determine the part weight.
The raw material is applied to the part weight, and the cost of plastic, and part is calculated then the engineer estimates the cycle time in the molding cycle using their experience applying the number of cavities in the mold and the cost of labor and press per hour, the labor charge is calculated.
Each order will have a minimum set-up charge spread over the quoted quantities. Other additions such as secondary operations may add operations packaging and sales commissions to the price.
The price for a part would be represented in different quantity breaks because of the set-up cost and sometimes because of the change in the cost of raw material given larger quantities.
If you would like to compare pricing from several molders, be sure to ask the molders to disclose the cost per pound of raw material, number of cavities in the mold, estimated cycle times, and estimated part weight.
You can create a spreadsheet to compare all the information. A molder that will not provide details in their quotations should raise questions in your mind.
Keep in mind that the low bidder may not always be the best, be sure to ask for a price guarantee.
Process for injection moulding near me, and you
Injection molding is a complex process that involves the injection of a polymer into a mold, where it is shaped into the desired shape. This process consists of four stages. These stages are clamping, injecting, cooling, and ejecting.
-
Clamping
The mold has to be closed before the material is injected to flow inside the mold. So, first, it is closed through a clamp unit. Both halves are attached to the injection molding machine, and one half (core side) can slide.
When the mold has been closed, it is clamped by the clamping unit by which the halves are kept tightly together. It takes longer for larger machines to close molds that have more clamping power, so in most cases, it will take slightly longer to close a mold as well.
-
Injection
Plastic pellets are fed into the injection molding machine through a large hopper. These pellets pass into the injection unit, which mixes them with the surrounding heat and pressurized air. The temperature of the surrounding barrel and the pressure helps to melt the pellets.
The injection time of plastic is measured by the volume of material injected and is calculated when 95%-98% of the mold is filled. Getting the injection process exact is difficult because the flow of plastic is constantly changing and dynamic.
Other factors such as injection pressure can also be used to estimate the injection time. An injection pressure meter can measure from 35-140 MPa. An injection time and the maximum pressure will be predicted and controlled by the hydraulic system in the machine.
-
Cooling
After the plastic inside the mold starts to cool and harden, it will form the desired shape. During the cooling process, the plastic may shrink slightly. Only after this period has passed, the mold can be opened.
Wall thickness and the thermodynamic properties of the plastic can determine the cooling time of the part.
-
Ejection
When the mold opens, the part is pushed out utilizing force as the part shrinks and will stick to the mold. After the mold is closed again, another injection can be made to restart the process.
Mold design is a critical factor in ensuring that the end product is of high quality.
The plastic mold has to be stable and capable of withstanding the pressures during the injection process. This is because the strength, durability, shape, and size of injected parts will depend on the type of mold selected.
The polymer must also behave properly as it flows along with the mold, and the mold must also be carefully designed to permit heat transfer that regulates the cooling process.
It is a complex operation requiring highly trained personnel to ensure the entire process is carried out. Therefore, keeping productivity high is imperative, and the safety of the workers is a primary concern.
Injection Molding Component Design
There are several basic concepts in component design that, if followed, will help to relieve many of the problems that beset the injection molder. Among these are:
- Maintain the wall thickness as uniformly as possible.
Differences in only 15-25 percent thickness will often lead to sinking marks in the thicker parts.
The thick wall could produce the worst voids, and these could affect the performance.
A stepped section can often impart rigidity (cf. corrugated roofing sheets). Even box sections are made more rigid while keeping their thickness even by slightly rounding the corners.
If ribs and bosses are to be introduced, sink marks may occur and may be difficult to avoid.
A useful rule is to make ribs only two-thirds of the general wall thickness and to design bosses similarly, causing holes to penetrate one-third of the depth into the wall.
- The wall thickness should be no greater than is necessary to give the strength and rigidity needed.
This keeps the use of material to a minimum and provides the shortest possible time cycle. Careful use of multiple gates can probably solve mold filling problems.
- Undercuts and re-entrant shapes cause extra costs both in mold production and in molding time (side core operation very often increases the time cycle)
They can often be avoided by the use of simple assembly methods applied to two or more components.
One of the most favored of these is the interference fit in which one component has a clip or other device which engages strongly with the other part and holds the two together (cf. the poppet bead).
Welding by friction, hot plate, or ultrasonic means can also be used, but in general, cementing with solvent or solvent-based adhesives is not recommended for the custom molder because of fire and toxicity hazards and problems of solvent recovery.
- Avoid the use of molded-in inserts if possible.
Use instead staked or spring-clip inserts into blind holes, which are easier to make by injection molding.
Insert molding is often very wasteful of time, both operator and the machine, which is generally the most expensive part of the process.
- Give the most generous radius possible.
Sharp corners, both external and internal, are natural stress-raisers. Still, a radius of 0.06 in (1 -5 mm) will significantly relieve the situation and increase impact strength by five or ten times.
Injection molding component designers may call for something difficult to mold. As the producer of a well-known brand of hand-tool manufacturers put it in an advertisement: “Occasionally, so rarely, in fact, ,that one feels rather guilty about mentioning it, designers have been known to create things which are just a teeny-weeny bit difficult to make.
Designers may be working in a state of ignorance—ignorance of the service conditions of a component, ignorance of the service performance of a material, and ignorance of the many factors involved in proceeding from component design to complete plastic molding.
There is a need for education, but there is a need for consultation and cooperation even more. Regular liaison between the end-user, component designers, mold designers, and molding technologists will prevent many of these problems from arising.
Example of an approach to injection molding design:
1. Define the purpose and performance of the injection molding product.
2. Determine if the product has space and load limitations.
3. Define how the injection molding product will be exposed to environmental stresses during its intended function.
4. Choose two or three materials that appear to satisfy the environmental conditions and the strength requirements.
5. Perform several trials with different materials and geometries to evaluate their suitability for the application under consideration.
6. Conduct a thorough cost-effectiveness analysis of the trial designs. Determine different levels of performance and associated costs associated with each level of performance, as much as possible with the data available.
7. Determine the fabrication method that is most appropriate to the injection molding product design.
8.With the preliminary assessment, select the most logical alternatives and prepare a detailed product design.
9.Based on the detailed design of the final product, determine the probable design, the material, and the manufacturing process.
10. If required, construct a model for testing the product’s effectiveness.
11. Create prototypes.
12. Develop and test prototype products to determine if they serve the intended purpose.
13. Based on the prototype testing, the mold maker should redesign the product.
14. Test again.
15. Field tests should be conducted.
16. Add instructions on how to use the software.
17. Design ready
Injection Molding Troubleshooting
1. Short shot: The plastic parts made by plastic injection molding companies have irregular and incomplete edges. It usually occurs at the farthest point of the gate, the roots of thin and long ribs.
2, Shrinkage: Occasionally, a place: 1. when the material thickness is uneven, 2. thick section of injection molded part, 3. boss and rib section. Due to shrinkage, the plastic parts develop dent, uneven, and wavy under low light conditions.
3, Flash: A part edge with an extra thin layer of plastic is often found in the following locations: 1. Parting line; 2. Moving core; 3. Ejector pin position, boss position, hole position, snap location.
4. Bubbles: The bubbles on the plastic surface are of a different color from the surrounding colors and are typical: 1. bubbles caused by gas, air, and water-gas that are not released in time. 2. bubbles caused by shrinkage. The bubbles in the transparent part are particularly distinct.
5. Weld line: When multiple molten flow fronts coincide with each other, a deep weld mark appears on the surface of a plastic part. This most commonly occurs at the confluence of multiple molten flow fronts.
6, Burning: it is not a flat surface. It is usually dark or black spots; usually, they are found in sections where it is difficult to fill and trap the gas easily.
7, Black spots: black impurities are evident on the surface of the plastic parts, mainly caused by the use of mixed materials.
8. Discoloration: The slight difference in color between the actual plastic part and its required color is very apparent, and it is generally because the pigment is incorrect, the mix ratio is incorrect, or the mold is set at the wrong temperature.
9. Wrinkles: The plastic parts show wavy lines on the surface caused by the cooling of the resin flowing.
10. Deformation: The plastic parts have distortions, undulations, curves, and this is particularly common in the bosses, ribs, and round-shaped injection parts. These are especially common to PP injection molding.
11. Wrong materials: In contrast to the specified materials, the one here can be identified by checking out the packaging label, the density, the burning continuity, the color of the flame, the color of the smoke, and the length of flames.
12. Stick to the mold: Incomplete plastic part staying in the cavity, in contrast to short-shot, or due to the lack of designing the mold ejector system, the plastic part is hard to be ejected from the cavity, generally in thin-walled areas, bosses, and snaps.
13. Scratch: The surface of the plastic parts rub against the surface of the cavity during the ejection so that a lot of them have scratches on the surface.
14, Over-flow: It is caused generally by cavity damage and occurs on the active section, bosses, ejector pins, and parting surface.
Click for more information as to the injection molding troubleshooting.