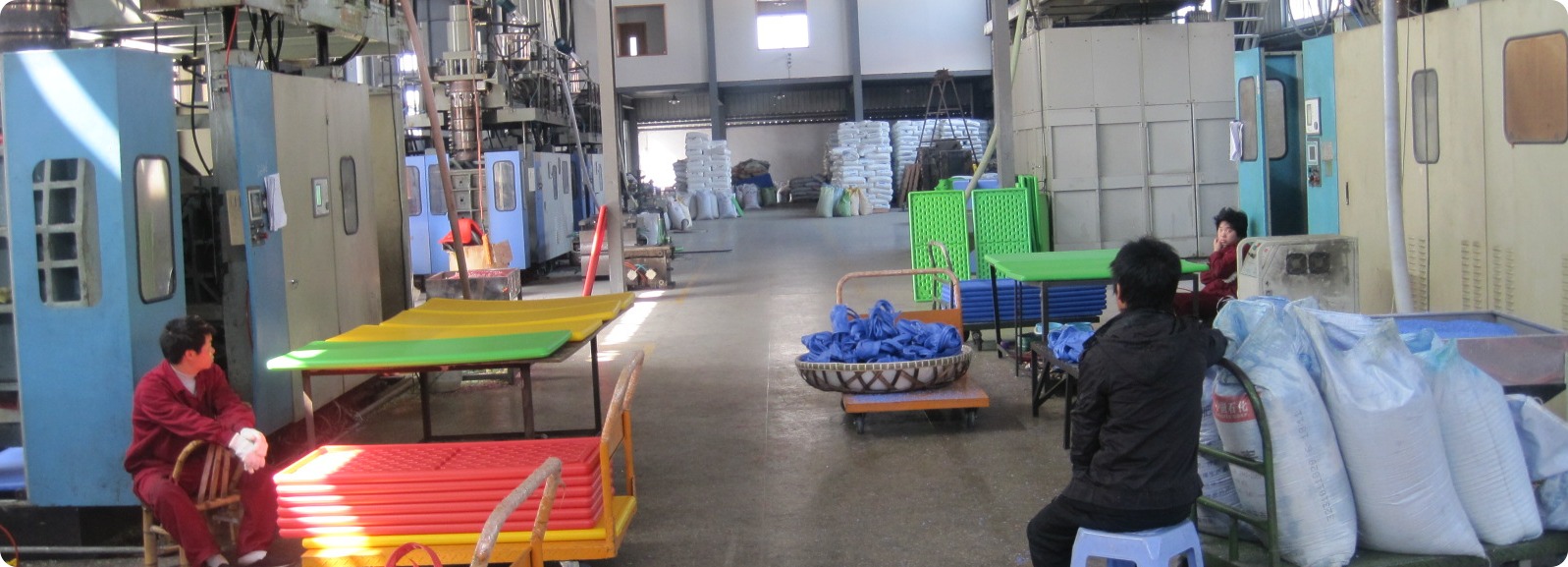
blow molded parts from China
Blow Molding Company
Topworks is a professional blow molded parts manufacturer from China. Our blow mold is integrated with engineering design and mold making, plastic injection and disassembly automation, which is suitable for high speed mass production, low cost and short delivery time. The all-round services covers pre-sale, sale during production and after-sales service.
Topworks has been in the plastic blow molded parts manufacturing industry for more than 10 years, which is a professional manufacturer that specializes in high-quality PET, HDPE,acrylic and polycarbonate blow molded parts. Our products include telecommunication product series, car accessories, healthcare product series and many others.
Blow molding, also known as hollow blow molding, is a molding way that the heated plastic parison gets inflated and molded in the blow mold to achieve blow molded parts, which are adopted to manufacture hollow products.
Blow molding is widely used in toys, household commodities, chemicals, cosmetics, food, etc. Our blow molded products include:
- toy car,
- teapot,
- toolbox,
- wheels,
- mineral water bottle,
- lampshade,
- pots, barrels,
- cans,
- pipeline,
- automobile conduit,
- hose,
- container,
- depot equipment,
- stadium seating, and so on.
Advantages: compared with injection molding, extrusion blow molding has the following advantages:
- Blow molding machine (especially blow mold) cost is low (similar product), blow molding machinery cost is about 1 / 3 – 1 / 2 that of the injection molding machine, also the production cost is low;
- In the blow molding, the heated parison is inflated in the blow mold under low pressure (mostly 0.2 – 1.0MN) via the die head on the blow molding machine. As a result of the small residual stress, the blow-molded parts have good performance: tensile resistance, impact resistance, bending resistance, and environment friendly. In the injection molding, the melted plastic should be injected in high pressure (15 – 140yPa) through the mold runner and runner, which will lead to uneven distribution of stress;
- The relative molecular mass of a blow-grade plastic (e.g., PE) is much higher than injection-grade plastics. Therefore, the blow molding product features the characters with high impact toughness, resistance to the environment, and stress cracking. So it is suitable for the production of packaging of transport detergent, chemical reagent container, and barrel;
- Because the blow mold is only composed of 2 cavities, simply adjusting the die head gap or extrusion conditions can change the thickness of the product. It is with advance to make the blow-molded part with the required wall thickness, which couldn’t be predicted. While for the injection molding, it is very hard to change the wall thickness of the injection molded product;
- Blow molding can produce products with very small wall thickness, which kind of products cannot be produced by injection molding;
- Blow molding can produce an integral, complicated and irregular product. While as to injection molding, to assemble two or more products, snap-fit, screw, and ultrasonic welding are needed.
The disadvantage of blow molding is that the accuracy of blow-molded products is generally not as high as injection molding products.
“I’m glad to inform you that all plastic parts are perfect!!! We are delighted, and therefore there are good chances to continue our relationship for any coming new project.”
CRISTIANO
ITALY
“Steven is a very detail-oriented project manager and engineer who can solve problems creatively and also provides excellent service. It was a pleasure working with him.”
DAVID
USA
In-house Blow Mold Making
One of the primary reasons for the rapid development of blow molding, once the equipment was commercially available,was the economies afforded a molder in the tooling costs.
Regardless of materials used, a blow mold consists of a set of pins and bushings for alignment of the two halves; pinch-off plates at both ends, usually made of mild steel, a basic mold body, or a shell;and adequate cooling channels for rapid and effective heat transfer.
Due to the limited number of blow mold and blow-molded part manufacturers in China, the molder must know as much about mold design and mold shrinkage as possible.
In a majority of cases, the initial development of a blow-molded item is done by the molder.
The part produced is actually a compromise between the molder’s machine capabilities and the customer’s desires.
For this reason, a molder must work extremely closely with the mold maker to make required changes and do all the testing before production.
Blow Molding Materials
The type of material selected for a mold will depend on:
- The number of pieces to be produced.
- Type of material to be blow molded.
- Several molds are required.
- Speed of production.
- Quality of the finished part.
Molds are presently produced from the following materials:
- Aluminum (cast and machined)
- “Kirksite” (pressure and gravity cast)
- Beryllium-copper
- Machined steel
Besides the four materials mentioned above, two others are being used to some extent in experimental work. They are:
- Epoxy filled with aluminum or steel.
- Hard copper shell molds.
Aluminum Molds
Aluminum molds are one of the most commonly used types.
In the cast aluminum type, the model maker produces a full-scale plaster model for customer approval.
These samples are either hand-made or machine-made, depending on the circumstances.
At this time, the model maker determines the shrinkage factor for casting (approximately .040″ per inch) and the shrinkage for the template of about .058-.060″ per inch for plaster and casting.
Once a model has been constructed, a plaster mold is produced, and from this is produced the first rough lead casting.
The lead casting is finished and dowelled, and used as the master for producing the production cavities. In some cases, cooling channels are cast into place during the casting operation;
in others, channels are drilled into the mold.
Since aluminum is relatively a soft metal, it is easily scarred or damaged by rough treatment in the shop.
Also, if used in constant production, the pinch-off areas degrade.
For this reason, a pinch plate of mild steel should be inserted to obtain maximum efficiency from the molds.
This is especially true of a mold whose shortest inside diameter is smaller than the parison diameter.
Zinc Alloy
This material, probably more commonly known as “Kirksite, “,is preferred by many molders because of its castability, stability, excellent heat transfer properties, machinability, and reasonable cost.
The grain structure of this type of mold gives a tensile strength of approximately 50,000 psi and compression strength of 100,000 psi.
The casting process is basically the same as for aluminum molds. These inserts accomplish three objectives.
- Since the pinch-off is the part of greatest wear, it can easily be replaced.
- It gives access to the mold for parting line finishing.
- It enables separate cooling to be installed in the pinch-off areas.
Zinc alloys can be cast, hobbed, or machined, and although they are more expensive than aluminum, they exhibit better heat-transfer characteristics and wear slightly better than aluminum.
Beryllium-Copper
Beryllium-copper molds are used extensively throughout the doll industry for the blow molding of doll bodies. This type of mold is roughly 2-3 times the cost of the equivalent aluminum mold but has excellent heat-transfer characteristics and, all things being equal, gives faster production.
Machined Steel
This type of mold is best used in two specific areas:
- If an article to be produced is within the diameter of the parison and an excess of material will result all around the molded piece, then steel should be used.
- In multiple-cavity blowing, again due to excessive pinch-off areas, steel is recommended.
The above types require extraordinary clamping pressure and result in more than normal wear on the pinch-off areas. The disadvantages of a steel mold are that the heat-transfer properties are only fair to good and that it is the heaviest of all mold materials and requires more set-up time than the lighter molds.