Regardless of whether the plastic mold you are using or storing needs to be repaired, there is a great deal of deterioration that will occur through its use or storage.
It becomes more damaging as it is used harder or kept longer.When damage occurs during operation, such objects include things like rusted or damaged core pins, corroded parting lines, and damaged gates. Damage in storage is often caused by corrosion.
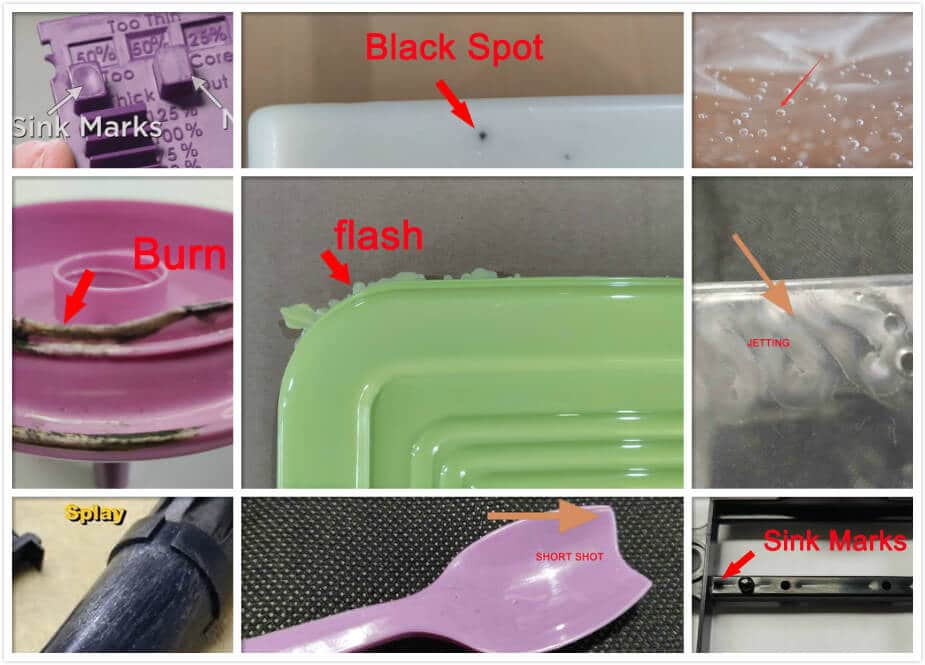
When any kind of operation is run, it is wise to save the final shot and keep it in a safe place with the mold.By showing how parts are designed, it provides a visible example for mold protection professionals.A technician can examine the units to identify the parting line condition, impression surface condition, and ejector pin location, among other relevant details. It would also be helpful to compile a list of the disorders that employees have noticed.
The cause of Damage
Most mold injuries can be attributed to inappropriate treatment.
The cavity may be damaged if you use steel screwdrivers to remove trapped units.
In addition to creating aesthetic flaws, this damage can also adversely affect measurements and make the molded component not tolerant.
It may create an undercut that causes subsequent units to catch and not be removed, or possibly even fracture. Lubrication can prevent shifting parts from galling, which will ultimately lead to components grabbing.
A poorly suited cloth can damage the highly refined mirror surface, even when cleaning the cavity surface.
If a process professional uses an excessive injection force at launch, for instance, and flashes the mold, incorrect handling results in severe damage.
This flash may force its way between bushings and leader pins, forcing the sidewalls out, or moving around slide mechanisms and cams.
As the mold opens, this can help hold it in place.
It is possible that nozzle drool could cause material to ooze onto the A part of the cavity set if it is produced.
In most cases, it is a thin plastic film that solidifies relatively quickly.
If the mold closes on the cavity, it can cause serious damage.
It is possible for a component of the mold to work with excessive temperatures if the mold temperatures are not handled properly.
Thermal expansion variants may occur if the discrepancy exceeds 15° F (6.5° C). Swelling can trigger.
—
After a mold has accomplished a certain volume of operation cycles (differing due to types of item and chemical being produced), it should be wiped clean to eliminate remains created in the molding procedure.
The cavity and venting fields display the main amount of remains; nevertheless, the ejector housing and runner blocks are other locations that accumulate residue.
As a result of restricted tolerances being controlled by the mold, this kind of residue accumulation could become so much to prevent the mold from shutting as it should and/or induce particular sizes, not intolerance.
Vent fields specifically call for particular attention.
If the venting failed (as a result of residue), they become useless, and excessive injection pressures will be necessary to fulfill the mold.
It might trigger flashing, which might end in mold deterioration.
As soon as the mold is taken away after production, it ought to be completely polished, examined, and sprayed (mainly interior, nevertheless lightly exterior) using a corrosion preventative chemical to reduce the chance of harmful corrosion development.
The covering ought to be specific in thickness for long-lasting (more than Four weeks) storage.
It is essential to drain the waterlines and clean them.
If possible, molds should be saved in a dried place to reduce corrosion-producing circumstances.
Fixing injury to a mold can vary from being a hassle-free procedure to incredible complexity regarding the gradation and types of deterioration.
A fix may need only to change a damaged ejector pin in a few circumstances, while in different circumstances, the whole cavity insert might need to change.
The tactic of restoration, then, is determined by what brought on destruction.
Getting rid of rust on the external surface is easy and generally will take only a good wire brushing for even severe circumstances.
On the other hand, getting rid of rust out of a cavity is known as an absolutely diverse scenario and may need welding and refinishing destroyed fields.
Additionally, the rust would have brought on a great deal of destruction that the cavity and several other parts may need to get replaced totally.
Molds cost a lot, and many factors harm them.
They need significant amounts of maintenance throughout their performance and storage stages.
Through maintenance and reduction in friction (and combined with good care and handling), Precautionary routine service will help reduce injury.
Planning for Repair and Protection
It is recommended that for substantial quantities or prolonged operations, the mold should be engineered to ensure that weak parts (like gate areas) could be conveniently changed or fixed.
This could be achieved by the employment of inserts and laminated structures.
Whilst this might be higher in price at the preliminary construction step, it offers an extremely easier fix method if such is necessary, and downtime will probably be reduced.
Eventually, the entire expense of mold protection tends to be reduced.
If a mold is intended for simplicity of fix, it will eventually work for considerably longer since welding will not be required for maintenance.
Welding may reduce the life span of a mold due to stresses and strains developed for the welding operation.
In setting up molds that include “sliding,” make sure you integrate easily available lubrication components (for example, grease fittings) into the motions design to make it simple for the molder to use lubrication on a scheduled basis.
Excessive quantity molds must also integrate lubrication strips in action fields leader pins and guided ejector plates to catch grease for longer lubrication performance.