O que são o sprue, o runner e o gate?
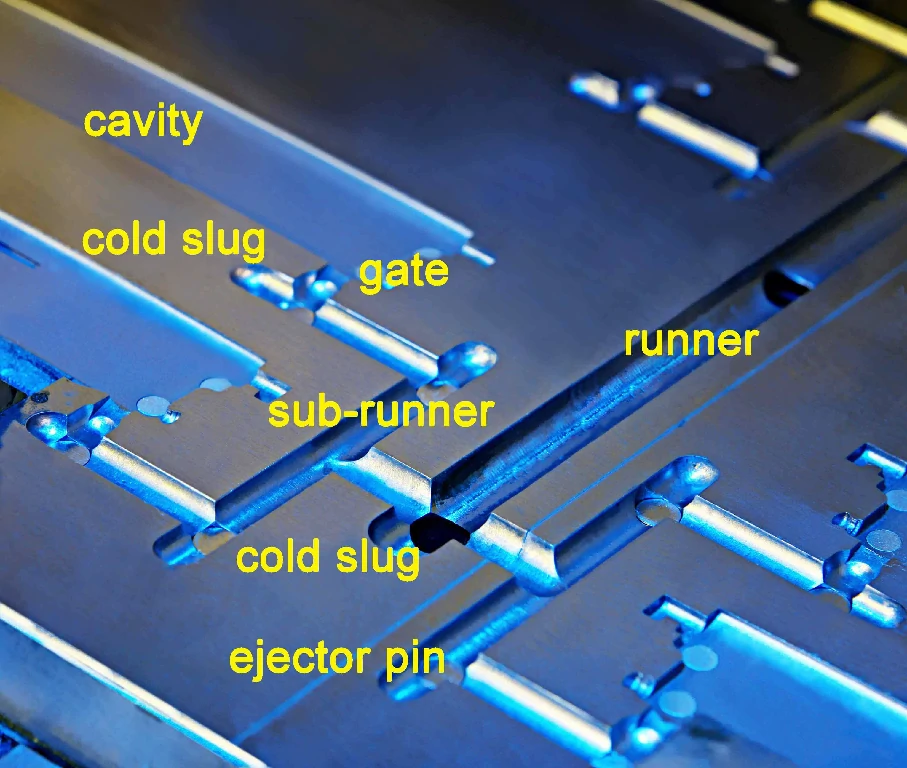
Tabela de Conteúdos
Os sprues, as corrediças e os gates cumprem a função de transportar o plástico fundido desde o bocal da unidade de injeção até às cavidades individuais.
Embora seja verdade que estes materiais plásticos podem ser reutilizados sob a forma de material reciclado, a sua presença significa, no entanto, uma redução do desempenho da máquina de moldagem por injeção, uma vez que têm de ser plastificados no cilindro.
Com peças mais pequenas, podem representar 50 % ou mais do peso real do tiro.
Tubo
O canal de entrada pode ser considerado a continuação do molde até ao bico da máquina de injeção.
Diz-se que os moldes de cavidade única em que o canal de entrada se liga diretamente à peça moldada têm um canal de entrada direto.
Muitas vezes, o desempenho de um molde de injeção de cavidade única é determinado pelo tempo de arrefecimento deste jito.
Para além de proporcionar um arrefecimento adequado do casquilho de jito, o diâmetro da abertura mais pequena do casquilho de jito deve ser mantido tão pequeno quanto possível e permitido pelo enchimento adequado da cavidade.
Não podem ser dadas aqui regras universalmente aplicáveis, uma vez que o preenchimento da cavidade depende de muitos factores.
O sprue deve ter uma inclinação de 1,5°.
Um rascunho maior pode simplificar a remoção da bucha do sprue, mas uma função do comprimento do corredor, pois pode-se supor que a perda de pressão em um corredor aumenta pelo menos proporcionalmente ao comprimento.
Com toda a probabilidade, provavelmente aumentará mais do que proporcionalmente, uma vez que a secção transversal é reduzida pela solidificação da massa fundida ao longo das paredes, e tanto mais quanto maior for a distância do jito.
Uma vez que o sistema de canais de entrada e saída representa perda de material e perda de capacidade de plastificação, os canais devem ser concebidos para serem tão curtos quanto possível e com a menor secção transversal possível.
O comprimento das corrediças é determinado pelo número de cavidades no molde e pela disposição geométrica das cavidades individuais.
Corredor
Os canais seguem os canais cortados na linha de partição em vez dos sprues, que entregam o material no centro da placa do molde. O seu design afecta a qualidade da peça e a eficiência do molde.
As corrediças mais grossas podem tornar as pressões de enchimento demasiado elevadas e causar tempos de ciclo longos indesejados. Por outro lado, os canais mais grossos podem causar um prolongamento desnecessário do tempo de ciclo e um aumento dos custos associados à retificação. A conceção ideal do canal deve encontrar um equilíbrio entre a viabilidade do molde e as pressões de enchimento.
Durante o enchimento do molde, o congelamento ocorre quando o calor da fusão é transferido para o molde. O resultado é um menor fluxo de material de fusão através do canal e uma grande queda de pressão. Os canais redondos criam a área de secção transversal mais pequena da parede congelada.
Uma corrediça trapezoidal pode ser uma alternativa mais eficaz do que as corrediças redondas porque só requer maquinação numa metade do molde. Os canais redondos requerem a combinação e a baixa restrição de fluxo de duas metades do molde.
Secções transversais do corredor
O sistema de canais num molde de injeção é responsável pela distribuição do material fundido desde o ponto de injeção até às várias cavidades do molde. A secção transversal do sistema de canais refere-se à forma e configuração dos canais e passagens que constituem o sistema de canais.
Mais de 35% da pressão necessária para encher o molde é frequentemente atribuída ao sistema de canais. Para eliminar esta queda de pressão adicional, optimize o percurso para cada porta. Por exemplo, substituir caminhos diagonais ou reorientar a cavidade para encurtar o canal.
Factores como a espessura do canal, a densidade da embalagem e o volume do canal têm um impacto direto na pressão de enchimento e no tempo de ciclo. Para determinar o diâmetro ideal do canal, muitos factores têm de ser considerados. Estes envolvem o volume das peças, a velocidade de enchimento, a pressão de enchimento, o comprimento do canal e a viscosidade do material.
- Para assegurar um acondicionamento adequado, efetuar corrediças que tenham pelo menos a mesma espessura que a espessura nominal da parede da peça.
- Para canais longos e sujeitos a elevados caudais volumétricos, aumentar a espessura do canal.
- Para as resinas semicristalinas, os canais devem ser mais pequenos do que para as resinas amorfas.
Corrediças para moldes de múltiplas cavidades
Os canais para moldes multi-cavidades são particularmente importantes. Um corredor deve ser bem concebido para que cada peça seja preenchida simultaneamente durante um único disparo num molde familiar.
Ajustando as localizações das comportas e/ou os comprimentos e diâmetros das secções do canal, é possível obter um fluxo equilibrado para cada cavidade, reduzindo simultaneamente o empacotamento excessivo e a formação de bolhas nas cavidades que se enchem primeiro.
Para além de proporcionar um fluxo equilibrado entre cada cavidade, os moldes que produzem múltiplos da mesma peça devem também assegurar uma distância igual entre o bico da máquina de injeção e a porta em cada cavidade.
O corredor com raios é normalmente uma opção. No entanto, um corredor com raios pode não ser muito eficiente à medida que o número de cavidades aumenta devido ao espaçamento entre cavidades ou ao aumento do tamanho das cavidades.
Sempre que possível, é preferível dispor as cavidades em filas e não em círculos. Os canais são normalmente divididos em filas que consistem em canais de alimentação principais e canais de alimentação secundários nas extremidades do trajeto do fluxo.
Geralmente, o diâmetro do canal aumenta à medida que aumenta o número de cavidades nesse segmento de canal, uma vez que o caminho do fluxo para cada cavidade deve ter o mesmo comprimento e fazer o mesmo número.
Se a taxa de alimentação do molde for constante, a velocidade da frente de fluxo entre cada cavidade permanecerá constante. Se a prensa não conseguir manter uma velocidade de fluxo frontal adequada, o número de cavidades que podem ser moldadas simultaneamente pode ser limitado.
Um corredor artificialmente equilibrado pode produzir um corredor uniformemente cheio, reduzindo assim o volume do corredor. Estes canais podem ter segmentos de diferentes diâmetros ajustados para compensar as diferenças de comprimento dos segmentos dos canais.
Um corredor em escada, um dos desenhos de corredor artificialmente equilibrado mais utilizados, contém duas filas de cavidades num corredor primário que os corredores secundários de igual comprimento alimentam.
Tipicamente, os sub-canais destas cavidades são progressivamente mais pequenos para os caudais com a distância mais curta entre os sub-canais. Estes projectos requerem sub-canais suficientes para equilibrar o caudal utilizando diâmetros de sub-canais razoáveis.
Uma corrediça para moldes de três placas atravessa a placa intermédia perpendicularmente à linha de separação da cavidade depois de transportar o material ao longo da linha de separação corrediça-cavidade.
Projetando-se a partir do canal principal, as gotas cónicas são normalmente colocadas na superfície da peça através de portas pontuais.
As gotas no molde reduzem de tamanho à medida que se dirigem para a comporta a uma taxa de aproximadamente 0,5 polegadas por pé. Evite a utilização de gotas longas, uma vez que o cone pode causar uma espessura excessiva na junção do corredor.
É bastante comum que os moldes de plástico de três placas sejam construídos com uma placa de remoção e pinos de sucção ou algum outro dispositivo. Certifique-se de que estas características não impedem o fluxo de material.
Portão
O portão é uma intersecção estreita entre o canal principal e a cavidade do molde, e a intersecção é também a parte mais curta de todo o molde.
A sua função é fazer com que o plástico fundido entre rapidamente na cavidade do molde, o que é benéfico para o rápido enchimento da cavidade.
Após o enchimento, o portão é condensado primeiro para bloquear a cavidade, impedir que o plástico derretido caia e evitar que a queda de pressão da cavidade seja demasiado rápida.
Uma pressão de apoio insuficiente produziria furos de retração ou partes amolgadas na peça de trabalho.
Porta de borda
A porta de borda (porta de borda) representa a mais simples das projectos de portõesÉ fácil de fazer e, normalmente, uma fresa pode terminar este trabalho.
Embora seja fácil de produzir, as portas de borda são severamente limitadas devido ao enchimento deficiente.
Neste caso, a resistência global do produto plástico obtido é fraca e o acabamento da superfície também não é bom. A porta de borda é normalmente utilizada para requisitos de qualidade de peças plásticas que não são muito elevados ou produtos sem requisitos de aparência.
Para além disso, é necessário cortar o portão mais tarde, o que provocará cicatrizes feias.
As portas laterais são adequadas para a maioria dos produtos moldados por injeção e muitos plásticos (como PVC rígido, PE, PP, PC, PS, PA, POM, AS, ABS, PMMA, etc.), especialmente para moldes com múltiplas cavidades.
É importante notar que pequenas alterações na profundidade da porta lateral podem causar grandes alterações no fluxo do plástico fundido.
Por conseguinte, a dimensão do portão lateral tem uma grande influência na qualidade e na eficiência da produção.
- PRÓS:
1 fácil de separar do artigo moldado;
2 corredores solares mais curtos;
3 fácil processamento e fácil corte.
- CONS
1. A localização limitada, a longa distância entre o portão e a cavidade, por vezes, e a grande perda de pressão;
2. tiro curto para moldagem de plásticos pouco fluidos (como PC);
3. Os artigos moldados planos ou de grandes dimensões são fáceis de encontrar bolhas ou marcas de fluxo na superfície devido à pequena dimensão da porta;
4. guarnição do portão rígido e vestígios óbvios.
PEÇA DE PLÁSTICO | PESO /g | altura da porta/mm | largura da porta/mm | comprimento da porta/mm |
PEQUENO | 0〜5 | 0. 25 〜0. 5 | 0. 75 〜1.5 | 0. 5 〜0. 8 |
SAMLL | 5〜40 | 0. 5 〜0. 75 | 1.5〜2 | 0. 5〜0. 8 |
MÉDIO | 40 〜200 | 0. 7S〜1 | 2〜3 | 0.8〜1 |
GRANDE | >200 | 1 〜1.2 | 3〜4 | 1〜2 |
Porta do ventilador
A forma do portão em leque é gradualmente alargada desde o sub-corredor até à cavidade, como um leque.
É adequado para produtos planos, em concha ou em caixa. O padrão de fluxo e a tensão de orientação podem ser reduzidos.
A forma do produto determina o ângulo.
A secção transversal da porta não pode ser maior do que a secção transversal do corredor.
Este tipo de comporta pode ser utilizado para muitos plásticos, tais como PP, POM e ABS.
- PRÓS
1. Enchimento uniforme para evitar deformações do produto.
2. Reduzir as tensões internas e a deformação.
3. Um artigo moldado com uma boa aparência e quase sem fenómenos negativos.
- CONS
1.Acabamento rígido.
Design: espessura H = 0,25~1,5 mm; largura =L/4, deve ser superior a 8 mm
De facto, o portão em leque é um design alargado do portão lateral. É utilizado para a parte plástica de uma grande área.
A porta em leque foi concebida para reduzir o empeno do produto e melhorar o acabamento da superfície do produto.
Para obter uma melhor superfície, a área de contacto não pode exceder a secção transversal do sub-riacho.
Devido ao grande tamanho do portão, é difícil de aparar e o traço deixado não é pequeno.
Porta de membrana
A comporta de diafragma pode ser considerada uma forma especial de comporta anular e é utilizada principalmente quando o centro do produto tem um diâmetro superior ao do canal principal. Adequado para moldagem por injeção de PS, PA, AS, ABS.
- PRÓS
1. impedir as marcas de fluxo.
Maquinação de 2 canais eficaz.
3 igual à função da porta direta, menos perda de pressão.
- CONS
1. Portão difícil de remover.
2. Uma vez, apenas uma parte.
3. o centro do orifício do produto deve estar alinhado com o corredor principal.
A comporta de membrana ou de disco pode ser utilizada para componentes cilíndricos ou ocos quando é necessária concentricidade e resistência da soldadura.
Para equilibrar o enchimento do molde, recomenda-se geralmente um comprimento mínimo de terra do portão de 0,5 a 1,0 mm.
A remoção subsequente do disco do portão da moldagem tende a deixar uma borda fortemente recortada na borda do componente.
O posicionamento da porta no interior da moldagem permite reduzir as operações de acabamento pós-moldagem.
Porta de anel
As comportas de anel são normalmente utilizadas em moldes cilíndricos quando as dimensões internas são mais importantes do que as externas.
É maquinada uma "calha" de canal à volta da cavidade do molde e subsequentemente espelhada à volta do núcleo, e é maquinada uma terra que liga a calha à parede da cavidade.
A profundidade da terra do portão é normalmente determinada devido aos ensaios do molde; as terras pouco profundas prejudicam o controlo da embalagem da moldagem, enquanto que as terras demasiado espessas criam problemas de degradação e conduzem a um aumento dos custos.
Porta de raios (porta de estrela radical)
Os portões de raios podem ser utilizados em moldes que são frequentemente demasiado grandes para um portão de diafragma ou de anel.
Permitem a passagem de um maior volume de polímero do que qualquer um dos dois últimos modelos.
Neste caso, a precisão dos componentes e a resistência da soldadura são reduzidas em favor do rendimento volumétrico e do controlo da embalagem.
Esta conceção do portão é adequada para moldes cilíndricos de secção mais grossa com pesos de injeção elevados.
Os restos de portões grandes requerem normalmente uma operação de maquinagem para os remover após a moldagem.
Túnel ou porta submarina
A porta do túnel permite o desengorduramento automático da moldagem a partir do sistema de alimentação.
A porta é cortada do componente durante o ciclo de ejeção do processo de moldagem.
Os diâmetros das portas de túnel variam entre 0,5-0,8 mm para plásticos não reforçados e diâmetros maiores de 2 mm ou mais para materiais reforçados.
Devido à conceção enterrada da porta, a retenção de gás e a consequente queima da superfície de moldagem podem constituir um problema durante a utilização.
Tendo isto em conta, deve ser adicionada uma ventilação adequada a um molde que incorpore um design de porta de túnel.
Na superfície de moldagem é deixada uma cicatriz no portão, que aumenta de tamanho à medida que o terreno de corte do portão se desgasta.
Portão de localização
As portas de ponta para moldes de três placas variam em tamanho, desde diâmetros de 0,8 mm-2 mm para materiais não carregados até 2,5-3 mm para materiais carregados.
Esta conceção do portão permite igualmente o desengorduramento automático das molduras durante a utilização.
O terreno da porta é normalmente reduzido em tamanho para permitir uma rutura "limpa" aquando da separação do componente moldado.
A quebra do portão é conseguida puxando a corrediça por trás, geralmente por ventosas ou pinos de puxar enterrados na parte de trás da corrediça.
Como resultado da espessura reduzida da terra da porta, as portas pinpoint são facilmente danificadas e tendem a sofrer desgaste se os materiais carregados forem processados regularmente.
Portão de registo
O efeito de enchimento lateral do formato da comporta reduz a probabilidade de ocorrência de jactos ou vermes quando o fluxo de fusão sai da comporta.
As comportas são frequentemente utilizadas para comportar grandes molduras decorativas, como caixas ou estojos de instrumentos, por razões estéticas.
O padrão de enchimento uniforme produzido em torno da caraterística da patilha reduz os efeitos da distorção induzida por tensão ou empeno depois de a moldagem ter solidificado.
As características das patilhas são dispendiosas de remover das molduras e, por conseguinte, devem ser posicionadas em locais onde possam ser deixadas no componente ou ter uma função útil, por exemplo, como patilhas de retenção para pulverização de tinta ou fins de acabamento semelhantes.
Flash ou porta de filme
Na sua essência, o flash gate é uma extensão do fan gate.
Todos eles podem ser utilizados em peças planas ou de grande superfície. A deformação destas peças deve ser evitada tanto quanto possível.
Mas o processamento subsequente do flash gate será muito problemático. Tenha cuidado ao utilizá-lo.
Dicas de design de portões
(1) O a posição do portão deve ser selecionada na superfície de corte tanto quanto possível para facilitar a remoção e a maquinação do molde, pelo que é necessário adotar a porta lateral em vez da porta pontual.
(2) O a distância até à porta é tão igual quanto possível a partir de cada cavidadee criar o caminho de fluxo mais curto para que a massa fundida possa encher todas as cavidades simultaneamente no menor tempo possível.
(3) O a posição do portão deve ser selecionada na secção de paredes largas e espessas da peçaque é conveniente para a alimentação e contração da massa fundida.
Esta localização do portão não conduz a defeitos como bolhas e depressões de contração.
Quando a massa fundida entra na secção de paredes espessas a partir da secção de paredes finas, ocorre a reinjecção.
Isto fará com que a velocidade e a temperatura de fusão desçam subitamente.
(4) Evitar o portão perto do núcleo longo e fino para evitar que o fluxo incida diretamente sobre o núcleo, causando deformação ou flexão.
A alta temperatura, a alta pressão e o impacto frequente na pastilha fraca fazem com que esta fique dobrada ou mesmo partida.
A temperatura de fusão é elevada, a pressão é elevada e a frequência do impacto no inserto é grande.
Se a inserção for fraca, deve ser dobrada ou mesmo partida.
(5) se os requisitos de moldagem por injeção forem cumpridos, quanto mais pequeno for o número de portas, melhor será. Reduziria as marcas de soldadura.
Se tal for inevitável, as marcas de soldadura devem ser desenhadas na superfície sem importância do produto e nas partes não frágeis.
No entanto, recomenda-se a utilização de portas múltiplas para produtos grandes ou planos, para evitar deformações e disparos curtos.
(6) O portão deve ser benéfico para a ventilação do molde.
Depois de a massa fundida entrar na cavidade, a ranhura de ventilação (na superfície de separação) não pode ser bloqueada primeiro.
Caso contrário, o gás na cavidade não pode ser descarregado, o que afectará o fluxo de fusão e causará defeitos tais como bolhas, linhas de soldadura ou disparos curtos.
Ver figura: Se a alimentação for efectuada a partir de (a), a fusão bloqueará primeiro a superfície de separação, o que fará com que (b) fique preso.
(7) O a localização do portão não afecta o aspeto e a função do produto.
Tal como referido anteriormente, qualquer portão deixará vestígios na superfície do produto.
Para não afetar a aparência do produto, o portão deve ser colocado na secção oculta do produto.
No entanto, devido à forma das peças de plástico, o portão deve ser ajustado externamente.
Para o efeito, o portão deve ser bonito e a situação deve ser comunicada ao cliente com antecedência.
(8) O portão não deve ser nem demasiado grande nem demasiado pequeno.
Se for demasiado grande, a temperatura de fusão NÃO aumentará ao passar pela porta e não será fácil evitar o refluxo;
Se for demasiado pequena, a resistência será grande e ocorrerão defeitos como jactos, manchas turvas e o tiro curto.
O tamanho do portão é determinado pelo tamanho, geometria e tipo de produto plástico. A dimensão do portão pequeno deve ser tomada em primeiro lugar e depois corrigida de acordo com o resultado do ensaio no projeto.
(9) Num molde multi-cavidades com uma grande diferença de volume de enchimento, o equilíbrio de alimentação pode ser alcançado por ajustando a dimensão da largura da porta em vez da profundidade.
(10) O a secção transversal da comporta é 3%~9% da secção transversal do sub-reguladore a forma da secção transversal da porta é circular (porta pontual) ou retangular (porta lateral), e o comprimento da porta é de 0,5~2. 0 mm, a rugosidade da superfície não é inferior a 0,4 um
(11) No molde de porta lateral, deve ser evitado o fecho das válvulas de fecho, uma vez que o curso da massa fundida provoca uma perda acentuada de temperatura e pressão.
Quando é impossível evitá-lo, é necessário fazer uma inclinação na posição de alimentação da válvula de corte para reduzir a resistência ao fluxo da massa fundida.
(12)O número de portas: O número de portas depende do rácio entre o fluxo de fusão L e a espessura da parede do produto T. Geralmente, cada porta deve ser controlada a L/T = 50~80.
Em qualquer caso, o valor L/T não deve ser superior a 100.
Na conceção real, o número de portas deve ser ajustado de acordo com a forma do produto, a viscosidade do plástico de fusão e outros factores.
(13) A linha de soldadura causada pela posição do portão pode ser avaliada pela experiência ou pela análise do fluxo do molde, quer afecte o aspeto e a resistência do produto.
Se for o caso, pode ser adicionado um poço de água fria para resolver o problema.
(14) Deve ser colocado um poço de projécteis frios perto da porta (especialmente da sub-porta) e o puxador deve ser ajustado para facilitar a desmoldagem do corredor.
(15) A porta deve ser concebida de modo a permitir um enchimento rápido, uniforme e unidirecional do molde.
(16) A posição da porta deve ser tal que o ar na cavidade possa sair durante a moldagem por injeção. Caso contrário, causará disparos curtos ou marcas de queimadura.
(17) Se a localização do portão criar as linhas de soldadura, estas devem ser projectadas para uma posição adequada.
(18) A posição e a dimensão da comporta devem evitar o fluxo de jactos.
O portão pode ser alargado para remover o fluxo do jato, ou a posição pode ser alterada para fazer com que a massa fundida atinja a parede do molde.
(19)O tempo de condensação do portão é o tempo máximo efetivo de retenção da cavidade.
Se a comporta for corretamente concebida, o refluxo do material injetado pode ser evitado.
(20) A comporta deve ser projectada o mais curta possível para reduzir a perda de carga através da comporta.
(21) A espessura normal da comporta é de 50 a 80 por cento da espessura da parede acabada.
A espessura da porta de remoção manual é, por vezes, a mesma que a espessura da parede da peça acabada.
A espessura da porta de remoção automática é geralmente inferior a 80% da espessura da parede para evitar a deformação quando a porta é quebrada.
O diâmetro das extremidades dos portões e subportões é normalmente de 1 mm a 3 mm.
(22) Os materiais com enchimento de fibras requerem comportas maiores para reduzir a quebra das fibras à medida que o material passa através da comporta. As portas mais pequenas, como as subportas ou as portas pontuais, podem causar danos nas fibras durante o enchimento.
(23) O portão deve ser projetado com um tamanho pequeno no início do projeto, para que possa ser aumentado mais tarde, se necessário (porque é difícil reduzir o tamanho do portão).