Have you ever thought about how artificial intelligence (AI) can change the design landscape in injection moulding? The integration of AI into the design phase opens up new possibilities for efficiency, accuracy and overall product quality. As manufacturers and designers adapt to this technology, understanding the impact of AI on design is key.
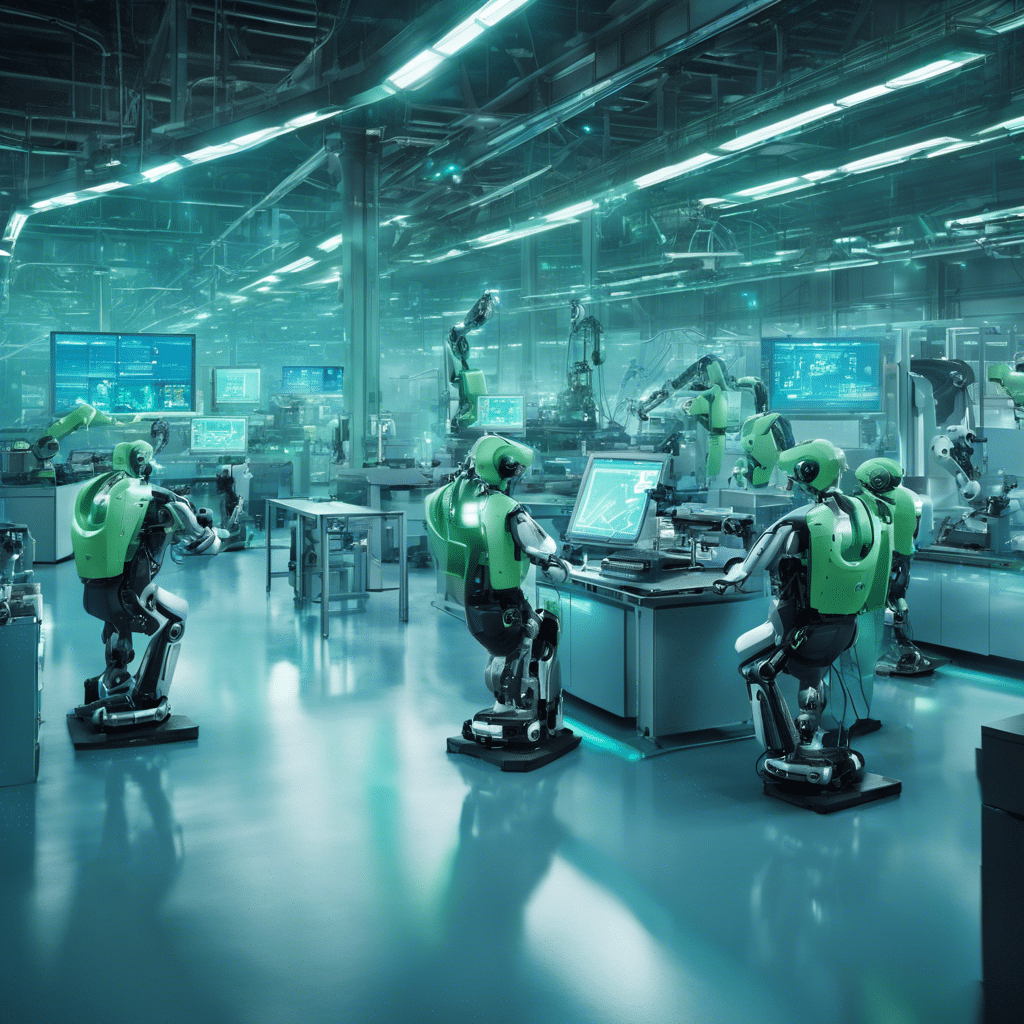
What is AI in Design
AI is the simulation of human intelligence processes by machines, especially computer systems. In design, especially in injection moulding, AI can process huge amounts of data, find patterns and propose design solutions much faster and more accurate than traditional methods.
Here is a summary table for injection molding design considerations:
Design Aspect | Considerations |
---|---|
Wall Thickness | does your design meet or exceed the nominal wall thickness? With a consistent wall thickness in the design, will your part cool evenly? |
Draft Angles | What’s your draft angle to the shrinkage you expect during cooling?Can your part be ejected from the mold easily with the draft angles you have? Are you going to stress your mold with your current design? |
Corners | Have the corners been radiused to avoid shrinkage, warping, shearing and/or breakage?How are all corners shaped in the mold so enough material can flow in and a consistent wall thickness is maintained? |
Undercuts | Can you remove any undercuts from the mold design without changing the function of the part?Can the mold be designed to accommodate the undercuts without going over budget? |
Resin Selection | Does the part design allow for proper flow of resin during injection and will it withstand the pressure required? What can affect the part’s cooling time, finish or other properties? How can you resolve those with changes to the part design and/or resin? |
Tolerances | How do your part’s tolerances affect the tooling (i.e. changing material for the mold, needing extra quality checks or more complex molds)? How can you address the performance requirements by redesigning the part/mold? |
AI in Design Benefits
- More Creativity: AI tools can generate multiple design options based on given parameters, so designers can explore solutions they may not have thought of.
- Quicker Prototyping: By using AI algorithms, designers can iterate faster, resulting in shorter design cycles and faster time-to-market.
- Data Driven Decisions: AI uses historical data to inform design decisions, so new products meet market demands and consumer preferences.
AI in Injection Moulding Design
1. Simplify the Design Process
AI technology simplifies the injection moulding design process.
- Generative Design: Using AI driven generative design software, engineers can input parameters such as materials, weight and strength and the software will generate design options. This results in optimised designs that meet functional requirements while minimising material usage.
- Design Validation: AI can simulate how designs will perform under different conditions, so teams can identify potential weaknesses and make changes before production starts.
2. Mold Design
Mold design is key in injection moulding and AI can help with this.
- Cooling and Heating Analysis: AI algorithms can analyse thermal dynamics during the moulding process, optimise cooling channel design. This results in uniform cooling, shorter cycle times and better part quality.
- Predictive Analysis: Using machine learning, manufacturers can predict potential issues with mold design, such as warping or sink marks, so changes can be made before physical prototypes are made.
Defect | Description | Solution |
---|---|---|
Sink Marks | Depressions or indentations on the surface of the molded part. | Increase gate size, adjust cooling time, add more pressure or modify part design. |
Warping | Deformation or twisting of the molded part after cooling. | Optimize cooling time, lower the mold temperature, or modify part design. |
Flash | Excess material present on the edges of the molded part. | Optimize clamping force, adjust injection speed, or modify tooling. |
Short Shot | Incomplete filling of the mold resulting in an incomplete part. | Increase injection pressure, adjust melt temperature, or change tooling. |
Burn Marks | Discoloration or burnt spots on the surface of the molded part. | Optimize cooling time, adjust melt temperature, or fix tooling. |
Voids | Empty spaces or air pockets within the molded part. | Increase injection pressure, higher melt temperature, longer holding time or change tooling. |
Flow Lines | Visible lines or streaks on the surface of the molded part. | Adjust injection speed, optimize gate location, or change tooling. |
Weld Lines | Weak bond lines formed when two or more flow fronts meet. | Optimize gate location, adjust melt temperature, or better tooling. |
Splay | Discoloration or streaking caused by moisture or contaminants. | Dry the material longer, lower melt temperature, or modify tooling. |
3. Quality Control
Quality control is crucial in injection moulding and AI helps with the mechanisms to ensure product consistency.
- Automated Inspections: AI driven visual inspection systems can detect defects in real-time during production, so only quality products reach the market.
- Machine Learning for Process Optimisation: By analysing production data, AI can find trends and suggest changes to improve quality outcomes. This means a proactive approach to manufacturing, reducing errors before they happen.
4. Automated Defect Detection
AI powered inspection systems use computer vision to detect defects during production. By looking at images of molded parts in real-time these can spot:
- Surface Imperfections: Scratches, dents or other surface defects that can affect product quality.
- Dimensional Errors: Parts that don’t meet spec, which can cause assembly issues.
- Color Variations: Inconsistent coloring that can mean material or process issues.
5. Predictive Maintenance
AI can help with predictive maintenance by analysing data from the machines to predict equipment failure before it happens. This proactive approach can reduce the chance of defects caused by faulty equipment. Key elements are:
- Data Monitoring: Continuously monitoring machine performance metrics like temperature, pressure and cycle times.
- Failure Prediction: Using historical data to predict when a machine needs maintenance, reducing unexpected downtime.
- Optimising Maintenance Schedules: Adjusting maintenance routines based on real-time data not fixed schedules.
6. Process Optimisation
AI can optimise the injection moulding process by adjusting various parameters in real-time to quality. This includes:
- Adaptive Control Systems: Automatically adjusting pressure, temperature and cooling times based on live data feedback to maintain optimal conditions.
- Feedback Loops: Closed loop systems that learn from past production runs to inform future settings.
- Material Quality Monitoring: Monitoring the quality of the raw materials and adjusting the process if inconsistencies are found.
7. Reporting and Analytics
AI can simplify the reporting and analytics of quality control and give more informed decisions. Key features are:
- Real-Time Reporting: Providing instant insights into production quality and potential issues, so you can respond quickly.
- Data Visualisation: Using dashboards to present quality metrics, so teams can see trends and areas for improvement.
- Error Analysis: Automatically categorising defects to find the root cause and recurring issues, so you can address them systematically.
8. Continuous Improvement
AI enables a culture of continuous improvement by giving teams the tools to find areas to improve. This means:
- Root Cause Analysis: Using AI to find the underlying causes of defects and inefficiencies so you can target improvements.
- Feedback Mechanisms: Processes where production staff can give feedback that AI tools can analyse for trends.
- Benchmarking: Continuously comparing performance against industry standards or historical data to drive improvement.
By incorporating AI into quality control, manufacturers can achieve more consistency and reliability in their products and ultimately better customer satisfaction and less costs for defects and rework.
AI with Design Software
AI Tools for Injection Moulding Design
- Autodesk Fusion 360: This platform combines CAD and CAM with generative design capabilities, so users can create optimised designs based on given parameters.
- SolidWorks with AI: Adding AI to SolidWorks gives design suggestions and enhances simulation, so engineers can validate designs earlier in the process.
- PTC Creo: PTC’s Creo platform uses augmented reality and AI to help designers visualise and iterate on their designs more effectively.
AI Design Challenges
While the advantages of AI in injection moulding design are clear, there are challenges to consider:
- Initial Investment: Implementing AI technology requires significant upfront investment in software and training.
- Data Quality: AI systems rely on good data. Bad or biased data will result in bad designs and decisions.
- Change Management: Moving to AI driven processes will meet resistance from teams used to traditional methods. Training and communication is key.
The Future: AI and Design in Injection Moulding
As AI technology advances, we’ll see more of this in injection moulding design:
- Real-Time Feedback: Future AI will provide real-time feedback during design, so changes can be made instantly.
- Collaborative AI: AI will enable a more collaborative design environment where multiple people can participate in the design process, regardless of location.
- Customised Solutions: AI will allow for more customisation in products, to specific customer needs without increasing costs.
Summary
AI will change injection moulding design in big ways. By boosting creativity, optimising mould designs and improving quality control, AI gives manufacturers the power to innovate and adapt in a competitive world. As companies adopt this technology, they’ll not only improve their designs but also be more efficient and cost effective.
For small and large manufacturers alike, AI in design is key to staying ahead. By embracing this technology you’ll open up new possibilities and be able to create products that are high quality and meet customer needs better.