In the world of manufacturing and industry, Industry 4.0 is a game changer that brings in new technologies into the production process. But what does that mean and why is it important? Industry 4.0 also known as 4IR uses the seamless connectivity of devices, systems and people to create smart factories that can produce goods more efficiently, flexibly and cost effectively than ever before.
According to a report by McKinsey & Company, companies that fully implement Industry 4.0 technologies can increase their productivity by up to 30% by 2030. Let’s get into this and see how Industry 4.0 changes traditional manufacturing practices and opens up innovation and productivity we never thought possible.
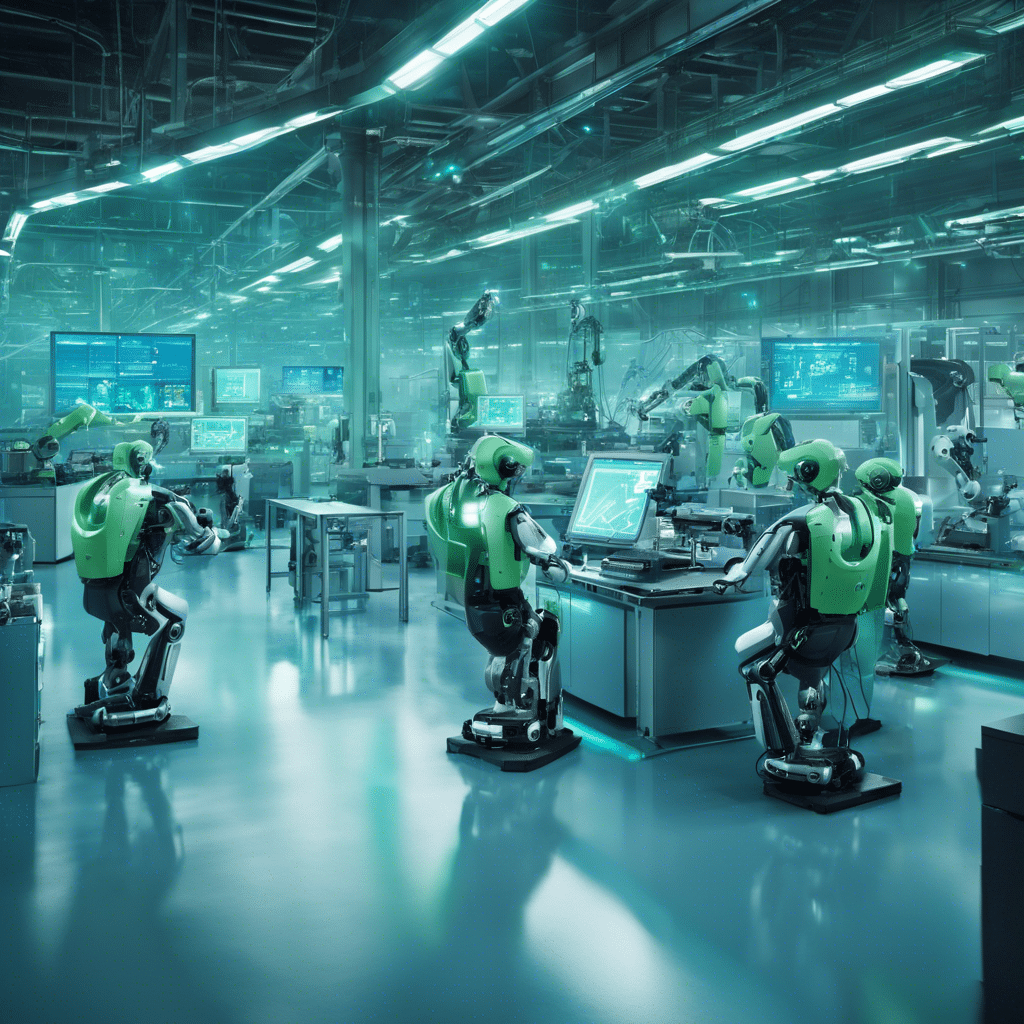
2. Historical Background
To understand Industry 4.0, let’s look back at its predecessors. The journey started with Industry 1.0 where mechanization through water and steam power happened in late 18th century. Then came Industry 2.0 where mass production happened with electricity and assembly lines. Industry 3.0 brought automation and computerization in late 20th century and was a significant technological leap.
These revolutions pave the way for Industry 4.0 which is driven by convergence of digital technologies. Imagine it as a relay race: each industrial revolution passes the baton to the next and technological innovations are the glue that binds them together. According to World Economic Forum, we are in the early stages of Industry 4.0 and significant investments and innovation will shape its future.
3. Industry 4.0 Technologies
At the core of Industry 4.0 are several key technologies that are changing the way industries work. Let’s break them down:
3.1 Internet of Things (IoT)
Internet of Things refers to the connectivity of devices and systems to communicate and share data. In a smart factory, sensors can monitor equipment conditions in real-time. According to Statista, there will be 30.9 billion connected IoT devices by 2025, that’s how big is the role of IoT in manufacturing.
3.2 Artificial Intelligence (AI)
AI is a key player in Industry 4.0 by analyzing data and automating decision making. According to PwC, AI can contribute up to 15.7 trillion USD to the global economy by 2030. That’s how big is the impact of AI to industries including manufacturing.
3.3 Big Data and Analytics
With the massive amount of data in manufacturing, big data and analytics becomes a must have. Companies that use big data can improve their operational efficiency by up to 15%, according to Deloitte. This data driven approach allows manufacturers to get insights on production efficiency, customer preferences and market trends.
3.4 Advanced Robotics
Automation is further revolutionized by advanced robotics which can perform complex tasks with precision and speed. According to International Federation of Robotics, the global stock of operational industrial robots will reach 4 million by 2023 and that will boost production capabilities.
3.5 Blockchain
And finally blockchain technology ensures security and transparency in the supply chain. According to IBM, blockchain can reduce information discrepancies by 50% and improve traceability in the supply chain which is crucial for product reliability and safety.
4. Industry 4.0 Benefits
Industry 4.0 brings many benefits:
4.1 Increased Productivity and Efficiency
By integrating technologies, companies can boost productivity, reduce downtime and optimize resource use. For example, Siemens’ Digital Factory Division achieved 10% productivity improvement in just a year after implementing Industry 4.0 technologies.
4.2 Flexibility in Manufacturing Processes
Industry 4.0 enables agile manufacturing processes, companies can respond quickly to changing demands. This flexibility can reduce lead times, according to McKinsey can improve customer satisfaction and loyalty.
4.3 Better Products and Services
With real-time data and smart machines, quality control becomes more precise. According to Mintel, 75% of manufacturers believe smart technology will improve product quality so only the best products reach the consumers.
4.4 More Customization and Personalization
Consumers today want personalized products and Industry 4.0 makes it possible. Manufacturers can use data to offer tailored solutions and improve customer satisfaction and loyalty. According to Gartner, 65% of consumers expect personalized experience in their purchases.
5. Challenges and Risks
Despite the many benefits of Industry 4.0, companies must face these challenges:
5.1 Cybersecurity Threats
This number shows how sophisticated cybercriminals are and how vulnerable our digital infrastructure is. Organizations must prioritize implementing advanced security protocols, employee training and regular system audits to mitigate the risks. Governments and industries must work together to establish global standards and share threat intelligence so we can be one against cybercrime.
5.2 Skills Gap in the Workforce
As technology changes, so must the workforce. The skills gap is a challenge, 7 out of 10 executives cite finding skilled labor as a major obstacle to digital transformation, according to Deloitte survey.
5.3 Integration with Legacy Systems
Many companies run on legacy systems that may not be compatible with new technologies. This lack of integration can lead to inefficiencies and additional costs and hinder Industry 4.0 benefits.
5.4 Regulatory and Compliance
Not complying with these regulations can result to financial penalties, reputational damage and loss of consumer trust. To mitigate these risks, organizations must implement data management policies, conduct regular audits and provide ongoing training to employees. Using advanced technologies like encryption, access controls and threat detection systems can further strengthen data protection.
6. Implementation Roadmap
For companies that want to adopt Industry 4.0, a strategy is key. Here are the steps:
6.1 Current State Assessment
Identify the key stakeholders involved and communicate the objectives clearly to ensure everyone is aligned. Create a detailed plan that outlines timelines, resources and risks and get feedback from all parties involved.
6.2 Set Clear Objectives
What do you want to achieve with Industry 4.0—efficiency, cost reduction or product quality? Clear objectives will guide the implementation. A Boston Consulting Group study found that companies with a clear strategy are 3.5 times more likely to succeed in their digital transformation.
6.3 Training and Development
To bridge the skills gap, companies must invest in employee training. This investment will pay off; according to World Economic Forum, 54% of all employees will need re-skilling by 2022.
6.4 Phased Implementation
Industry 4.0 doesn’t have to be all or nothing. Start with pilot projects to test new technologies before scaling up. This will minimize risks and allow for adjustments along the way. Focus on areas that will give quick wins, efficiency improvement or downtime reduction.
Integrate advanced tools like IoT, AI and big data analytics gradually to improve decision making and processes. By taking small steps, organizations can build confidence, get valuable insights and have a smoother transition to full scale implementation.
7. Examples and Case Studies
Several companies have already implemented Industry 4.0 initiatives:
7.1 Siemens
Siemens has integrated IoT and AI in their manufacturing processes and achieved significant efficiency gains. They collect data from machines and optimize production schedules and reduce downtime. Their initiative has reportedly increased productivity by 10-20% across their factories.
7.2 General Electric
GE uses advanced analytics in their manufacturing plants for predictive maintenance. This foresight prevents equipment failures, saves costs and increases productivity. GE estimates their predictive maintenance has saved them 1 billion USD annually.
7.3 Bosch
Bosch has a holistic approach to Industry 4.0, using smart factories to maximize efficiency. Their connected devices improve collaboration across the supply chain and reports show 25% operational efficiency improvement.
8. Next
What’s next for Industry 4.0? Here are a few predictions:
8.1 Technological Advancements
We will see rapid progress in AI, machine learning and robotics leading to even more complex manufacturing processes. For example, the global AI market is expected to grow from 27 billion USD in 2020 to 390 billion USD by 2025 according to MarketsandMarkets.
8.2 Global Economic Shifts
Industry 4.0 will reshape global economies and impact job markets as roles will evolve to fit the new technological landscape. A McKinsey report says automation will displace 15% of the global workforce by 2030 but will also create new job opportunities that require different skill sets.
8.3 Sustainability
As sustainability becomes top of mind, Industry 4.0 will help optimize resource usage and reduce waste and drive green manufacturing. According to Capgemini, 80% of manufacturers believe smart technologies will lead to improved sustainability.
9. Summary
In summary, Industry 4.0 is not just about keeping up with technology; it’s about the future of manufacturing. As companies get ready for this change, they must be proactive to understand and integrate. The opportunities are big, so are the challenges.
Let’s do this—invest in technology, skills and processes today for tomorrow.
FAQs
1. What is Industry 4.0?
Industry 4.0 is the integration of digital technologies into manufacturing processes to create smart factories that improve efficiency, productivity and customization.
2. How will Industry 4.0 impact employment?
Industry 4.0 will displace some jobs but will also create new opportunities that require technology and data analysis skills.
3. What are the key technologies for Industry 4.0?
IoT, AI, big data analytics, advanced robotics and blockchain are the key technologies that enable connectivity, decision making and efficiency.
4. What are the barriers to Industry 4.0 for businesses?
Cybersecurity, skills gap, integrating new technologies with existing systems and regulatory compliance.
5. How do companies implement Industry 4.0?
Assess your current state, set goals, invest in employee training and pilot projects.