Injection Molding in Electronics: The Unsung Hero of 2025 Manufacturing
Intro: The Hidden Hero in Your Pocket
Did you know the sleek smartphone you’re holding right now owes its existence to a 70-year-old manufacturing trick? Or that injection molding—yes, the same process behind LEGO bricks—is now crafting AI-powered wearables and biodegradable AirPod cases? Let’s dive into why this unassuming tech is the Taylor Swift of electronics manufacturing: quietly iconic, endlessly adaptable, and absolutely everywhere in 2024.
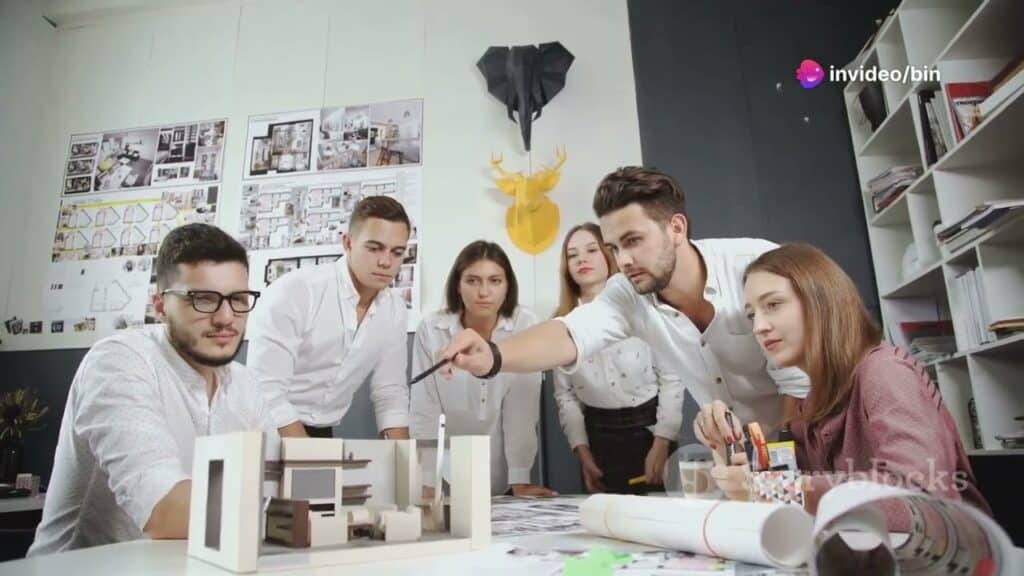
Why Injection Molding in Electronics is Dominating 2024
The Stats Don’t Lie:
- Over 20% of eBay’s 2024 electronics sales involved injection-molded components (think: ergonomic gaming controllers, foldable phone hinges).
- Gartner’s 2024 tech trends report highlights “smart manufacturing” as a top priority, with AI-optimized molds reducing waste by 40% in pilot projects.
But Why Now?
- The “TikTok Effect”: Consumers demand gadgets that are cheap, chic, and eco-friendly—all at once. Injection molding delivers precision at scale (hello, $10 wireless earbuds) while adapting to materials like algae-based bioplastics.
- AI to the Rescue: New tools like machine learning mold simulations cut prototyping time from weeks to hours. One factory in Shenzhen used this to launch a viral solar-powered phone case… in 11 days.
Top 3 Injection Molding Myths (Debunked with Memes)
1️⃣ Myth: “3D Printing Will Kill Injection Molding”
Reality: 3D printing is the quirky artist; injection molding is the stadium-filling rockstar. While 3D printing excels at prototypes, molding still produces 90% of mass-market electronics (with 1/10th the cost per unit).
2️⃣ Myth: “Eco-Friendly Molding is a Greenwashing Gimmick”
Reality: Brands like Fairphone now use 30% recycled ocean plastics in phone casings. Bonus: A 2024 study found biodegradable PLA resins can now withstand smartphone heat without melting (take that, skeptics).
3️⃣ Myth: “It’s Just for Basic Plastic Parts”
Reality: Today’s molds create nanoprecision components for AR glasses and medical sensors. One company even molded a transparent, conductive antenna for 6G routers—no assembly required.
How to Future-Proof Your Electronics with Smart Molding: 5 Pro Tips
- Embrace the “Ugly” Prototype Phase
- Use AI tools like Autodesk Moldflow to simulate stress points before cutting metal. One startup avoided a $50k mold redesign by spotting a airflow flaw in VR.
- Design for Disassembly
- Apple’s 2024 “E-Waste Reduction” initiative? All injection-molded parts snap apart without glue. Pro tip: Add micro-latches for easy recycling.
- Hop on the Hybrid Materials Train
- Mix carbon fiber-reinforced polymers for drone frames or self-healing silicones for workout earbuds.
- Small Batches, Big Wins
- Platforms like Topworks now offer low-minimum mold runs (500 units) for indie gadget makers.
- Steal This Viral Marketing Trick
- Boost sales by sharing your molding process on TikTok. A headphone brand went viral showing how rainbow-swirl ear cups get their color.
Conclusion: The Mold That Shapes Tomorrow
Injection molding isn’t just about plastic—it’s about possibility. Whether it’s enabling AI-driven smart homes or keeping e-waste out of landfills, this “old-school” tech is the quiet force behind 2024’s coolest gadgets.
CTA: Loved this? Hate plastic? Let’s debate! Drop a comment: Should all injection molding go biodegradable by 2030?