Automotive parts have to meet strict standards of quality, durability and performance and injection molding is becoming a key manufacturing technique to meet these demands. From intricate interior trims to underhood parts – injection molding provides precision, versatility, cost efficiency – it’s a must have for modern vehicle production.
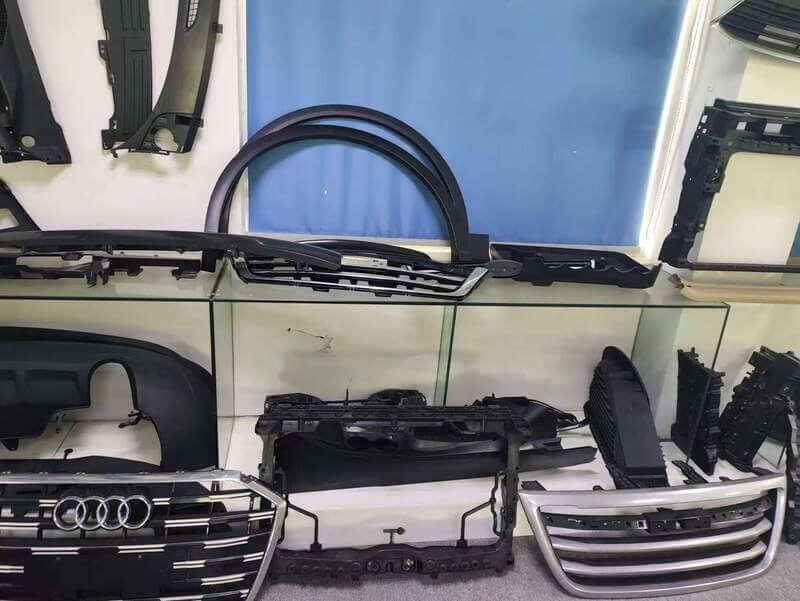
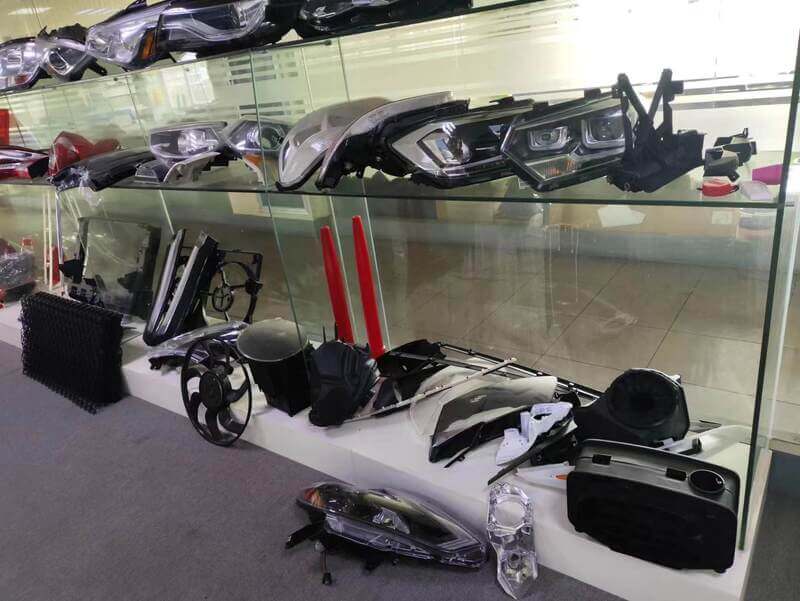
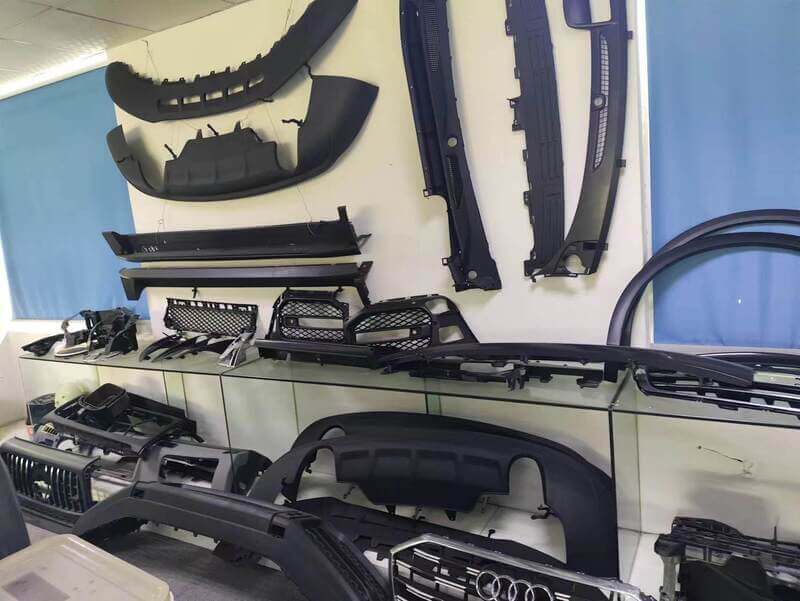
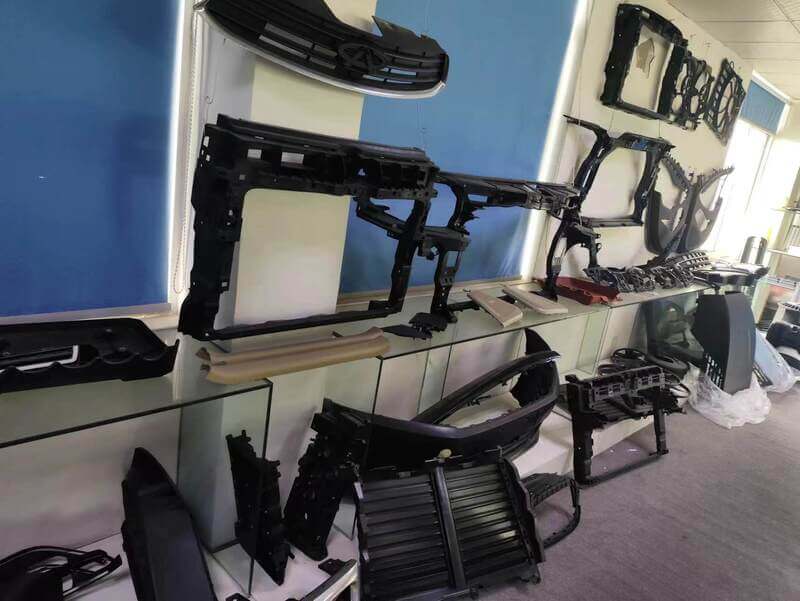
Advantages of Injection Molding for Automotive Applications
consistency and repeatability
One of the strengths of injection molding is its consistency and repeatability in producing parts thanks to engineered molds and controlled processes. Companies using injection molding ensure each part meets specifications so there’s less variability and less risk of defects – something critical in automotive where small deviations can compromise safety, performance or aesthetics. This level of repeatability is key.
High Volume Production
Injection molding offers automotive manufacturers economies of scale and cost efficiency through high volume production. Once the initial tooling and setup costs are covered, producing large quantities of parts is cost effective and fast – exactly what injection molding is all about in this industry. Automotive companies that need thousands of components to meet global demand can take full advantage of injection mold’s scalability to their benefit.
Material flexibility
Injection molding’s flexibility goes beyond manufacturing capabilities; a range of thermoplastic materials from engineering grade polymers to thermoset resins can be used in the process, giving automotive manufacturers plenty of options to choose from for specific applications that meet performance, durability and safety regulations.
complex geometries
Automotive parts require complex geometries with tight tolerances, precise dimensions and flawless surface finishes. Injection molding excels in these areas by producing parts with exact dimensional accuracy and spotless surfaces – from complex dashboard assemblies to aerodynamic body panels requires precise manufacturing for maximum quality results from injection molding processes.
surface color flexibility
Aesthetics plays a big part in automotive design and styling and injection molding offers many color options to meet these aesthetic standards. By injecting colorants or pigments into the molten resin during the injection molding process, manufacturers can produce parts in any desired color or create special effects like metallic and pearlescent finishes that match the overall vehicle styling and design. This flexibility allows parts to blend seamlessly with the vehicle design and style.
Injection Molding Materials for Automotive Parts
Material selection is critical to performance, durability and safety of automotive components. Many thermoplastic materials used for injection molding of automotive applications have different properties and benefits; each has its own advantages:
Acrylonitrile Butadiene Styrene (ABS) is the most popular material in the automotive industry due to its impact resistance, heat tolerance and colorability. ABS is often used in interior trim components – door panels, instrument panels and console assemblies where strength meets style.
Polyamides, also known as nylons, are known for their strength, abrasion resistance and thermal stability – properties that make polyamides ideal for underhood applications like air intake manifolds, engine covers and transmission components as they can withstand high temperatures and harsh environments.
Poly(Methyl Methacrylate), commonly referred to as acrylic, is an opaque thermoplastic known for its optical clarity and weatherability. PMMA can be found in automotive components like taillights and turn signal lenses as well as interior parts like instrument cluster lenses and decorative trim pieces, weatherproofing. In the automotive industry specifically, PMMA is used as exterior lighting components like taillights or turn signal lenses and widely used in interior components like instrument cluster lenses or decorative trim pieces.
Polypropylene (PP) Polypropylene is an economical material with good chemical resistance and impact strength used in automotive components like battery casings, exterior trim parts and fluid reservoirs due to its light weight, durability and affordability.
Summary
With the automotive industry’s standards on precision, performance, cost and aesthetic customization injection molding has become a must-have process. By utilizing its repeatability, scalability, material flexibility and high precision customization injection molding can produce automotive parts that meet industry requirements.
Automotive injection molding offers automotive manufacturers a total solution from interior trims and exterior body panels to critical underhood components. As the industry moves towards lightweighting, advanced materials and new designs – injection molding will be part of it.
From Injection Molding for Automotive Part Production:
Injection molding provides repeatability in terms of quality control and defect elimination in automotive part production making the process cost efficient and high volume production suitable to the scale of the auto industry.
ABS, polyamides, PMMA and polypropylene thermoplastic materials can be used for injection molding for automotive.
Injection molding offers high precision, beautiful surface finishes and many color options that meet the aesthetic and performance requirements of the automotive industry.
As the industry evolves injection molding will still be needed to produce affordable automotive parts.
Table: Comparison of Injection Molding Materials for Automotive Applications
Material | Strength | Impact Resistance | Heat Resistance | Chemical Resistance | Typical Applications |
---|---|---|---|---|---|
ABS | Good | Excellent | Moderate | Fair | Interior trim components, instrument panels |
Polyamide (PA)/ Nylon | Excellent | Good | Excellent | Good | Engine covers, air intake manifolds, transmission components |
PMMA | Fair | Fair | Good | Excellent | Exterior lighting components, instrument cluster lenses |
Polypropylene (PP) | Good | Good | Fair | Excellent | Battery casings, exterior trim parts, fluid reservoirs |
This table provides a comparative overview of the properties and typical applications of commonly used injection molding materials in the automotive industry, highlighting their respective strengths and suitabilities for various components.