Why Choose Cost Effective Injection Molding Solutions?
The impact of optimized injection molding goes far beyond just cost savings. Our integrated approach delivers measurable improvements through process optimization and technology implementation. Through analysis and implementation of advanced manufacturing techniques we typically achieve 20-30% overall cost reduction. This is achieved through multiple optimization channels, material usage efficiency, cycle time reduction and automated quality control systems.
Material cost savings of 15-25% are achieved through advanced material selection and waste reduction techniques. This isn’t just about choosing lower cost materials, it’s about implementing material flow analysis to minimize waste during production. Our engineers work with material suppliers to find the optimal grade that meets performance requirements while reducing cost.
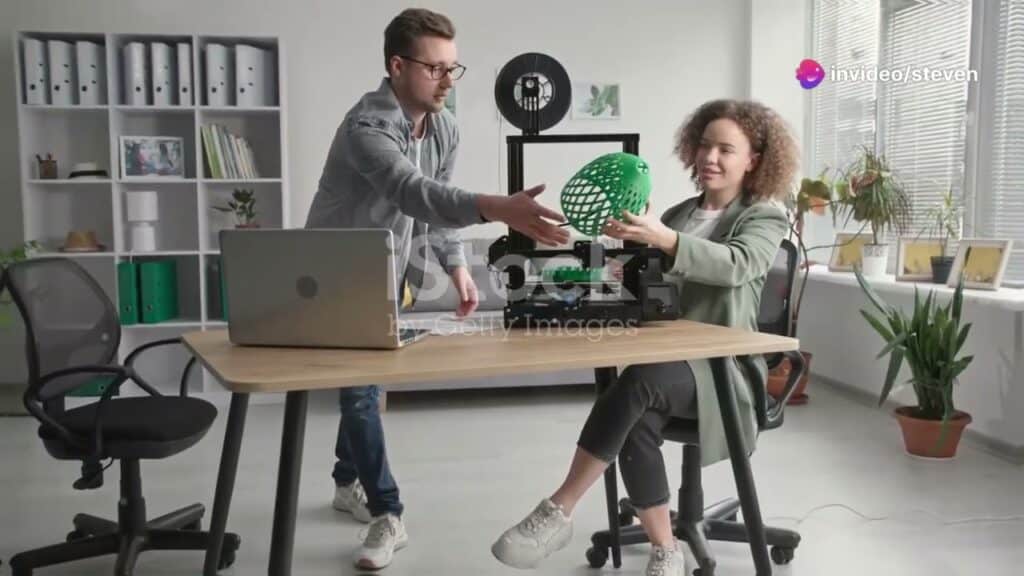
Time to market acceleration of up to 40% comes from our streamlined development process and advanced prototyping. This doesn’t just reduce direct costs, it’s a competitive advantage by getting to market faster and reducing inventory carrying costs.
Rapid Prototyping: new parts Development Faster and Save
Rapid prototyping is a critical part of cost effective manufacturing, it’s more than just a pre-production phase. Our prototyping process combines advanced CAD/CAM systems with state of the art 3D printing and CNC machining to produce functional prototypes that are a exact representation of the final production part.
The 48 hour turnaround for most prototype projects is achieved by optimizing our prototyping workflow. This includes parallel processing of design verification, material selection and tooling preparation. Our rapid prototyping facility runs 24/7 with automated systems to maximize efficiency.
Cost effective prototype molds are developed using advanced aluminum tooling techniques that reduce initial tooling cost while maintaining precision. These prototype molds are designed to be modular so we can make changes based on test results. Aluminum tooling for lower volume production can reduce initial tooling cost by up to 50% compared to traditional steel molds and produce thousands of high quality parts.
Smart Design: Your Maximum Savings
Design optimization is one of the most powerful ways to reduce cost in injection molding. Our Design for Manufacturing (DFM) analysis goes beyond basic manufacturability checks to find opportunities for big cost savings through smart design changes.
We start with a detailed analysis of part geometry, material selection and intended function. Our engineers use advanced simulation software to analyze material flow, cooling patterns and structural integrity. This often reveals opportunities for wall thickness optimization which can reduce material usage while maintaining or improving part strength.
Cooling system optimization is key to cost reduction. Through thermal analysis and simulation we design optimal cooling channel layouts that reduce cycle time. This often involves conformal cooling channels in tools which can reduce cooling time by up to 40% compared to traditional cooling methods.
Advanced Material Selection and Optimization
Material selection is where cost and performance meet. Our approach to material selection combines technical expertise with market knowledge to find the optimal material that balances cost and performance requirements. This isn’t just about choosing lower cost materials, it’s about understanding material properties, processing characteristics and long term performance requirements.
We use advanced material testing protocols to validate alternative materials to ensure they meet all performance specs while offering cost savings. This might involve using advanced fillers to reduce material cost while maintaining or improving mechanical properties or developing custom material blends that optimize both cost and performance.
Quality Assurance & Lean Manufacturing Integration
Industry 4.0 Quality Control
Our quality assurance system goes beyond traditional inspection based approach by integrating advanced statistical process control (SPC) with lean manufacturing principles. This combination creates a dynamic quality management environment that reduces cost and improves product quality.
At the heart of this is our Industry 4.0 approach to quality control. Real time data from the injection molding machines is fed into advanced analytics systems that can predict quality issues before they occur. For example our pressure curve analysis system monitors injection pressure in real time and automatically detects subtle variations that may indicate the early signs of quality issues. This predictive capability reduces scrap rate by 15-20% compared to traditional quality control methods.
Lean Manufacturing Implementation
Our lean manufacturing integration is about eliminating non value added activities throughout the production process. Through value stream mapping we have identified and eliminated common sources of waste in injection molding. For example our automated material handling systems reduce labor cost while ensuring precise material mixing ratios resulting in better part quality and less material waste.
Advanced Process Control and Automation
Modern injection molding requires advanced process control systems to be cost effective. Our facilities have advanced closed loop control systems that monitor and adjust critical processing parameters. This goes beyond basic parameters like temperature and pressure to include cavity pressure monitoring and automatic viscosity adjustment.
The use of artificial intelligence in process control has changed the way we approach optimization. Machine learning algorithms analyze historical production data to find the optimal processing windows and adjust the parameters to keep the conditions optimal. This smart automation has reduced setup time by up to 35% and cycle time by 12% across multiple applications.
Energy Efficiency and Sustainable Manufacturing
Sustainability in injection molding isn’t just about being green – it’s about cost reduction. Our energy management system integrates several innovative ways to reduce energy consumption while maintaining production.
We have implemented heat recovery systems that capture and reuse heat from the molding process, reducing overall energy consumption by up to 25%. This includes heat exchangers that transfer excess heat from hydraulic systems and barrel heating to facility heating or process water preheating.
Our servo driven hydraulic systems are another energy efficiency innovation. Unlike traditional hydraulic systems that run continuously, these smart systems only run when movement is required, reducing energy consumption by up to 50% compared to traditional systems. The precision of the servo drives also improves part quality by providing better pressure control during injection and holding phases.
Tool Design and Maintenance
Tool life and performance has a big impact on long term production cost. Our tooling strategy combines advanced design techniques with preventive maintenance programs to maximize tool life and minimize downtime.
We use wear analysis and simulation tools during the design phase to identify wear points and optimize tool steel selection. Critical wear areas are often enhanced with surface treatments or special insert materials to extend tool life by up to 300% in high wear applications.
Our preventive maintenance program uses IoT sensors embedded in critical mold components to monitor wear patterns and predict maintenance needs. This predictive approach has reduced unexpected tool failures by 85% and extended average tool life by 40% compared to traditional maintenance schedules.
Supply Chain and Inventory Management
Cost reduction in injection molding requires advanced supply chain management. Our integrated supply chain system uses analytics to optimize inventory levels and material purchasing strategies.
We have a dynamic inventory management system that adjusts safety stock levels based on historical usage and predicted demand fluctuations. This has reduced inventory carrying cost by 30% while maintaining 99.9% material availability.
Our supplier partnership program goes beyond traditional vendor relationships to create co-development opportunities. Through joint material development programs with key suppliers we have achieved cost reductions in several applications and improved material performance.
Project Implementation and ROI Optimization
Successful cost reduction requires good project planning and execution. Our project management approach combines traditional stage-gate methodology with agile principles to get projects implemented fast while maintaining control of the outcome.
We use financial modeling tools to evaluate cost reduction initiatives, not just direct savings but also secondary benefits like reduced cycle time, improved quality and reduced maintenance. This comprehensive analysis ensures that resources are allocated to projects with the highest return on investment.
Final words
The world of injection molding is changing driven by technology and market demand for efficiency. By implementing all the strategies and technologies in this guide manufacturers can achieve the 30% cost reduction and improve product quality and environmental sustainability.
We have seen over the decades that cost optimization in injection molding requires a holistic approach that covers multiple aspects of the process. The combination of advanced process control, smart automation, optimized tool design and quality management systems creates a synergy that delivers more than the sum of the parts.