The Search for Affordable Injection Molding Factories Includes Worldwide Assessments
The modern manufacturing industry requires companies to seek ways for reducing production costs while maintaining product quality standards. The critical manufacturing process of injection molding requires substantial investment from many companies who want to scale up their plastic component production. This article examines worldwide injection molding factories with cost benefits while providing essential information for your manufacturing strategy decisions.
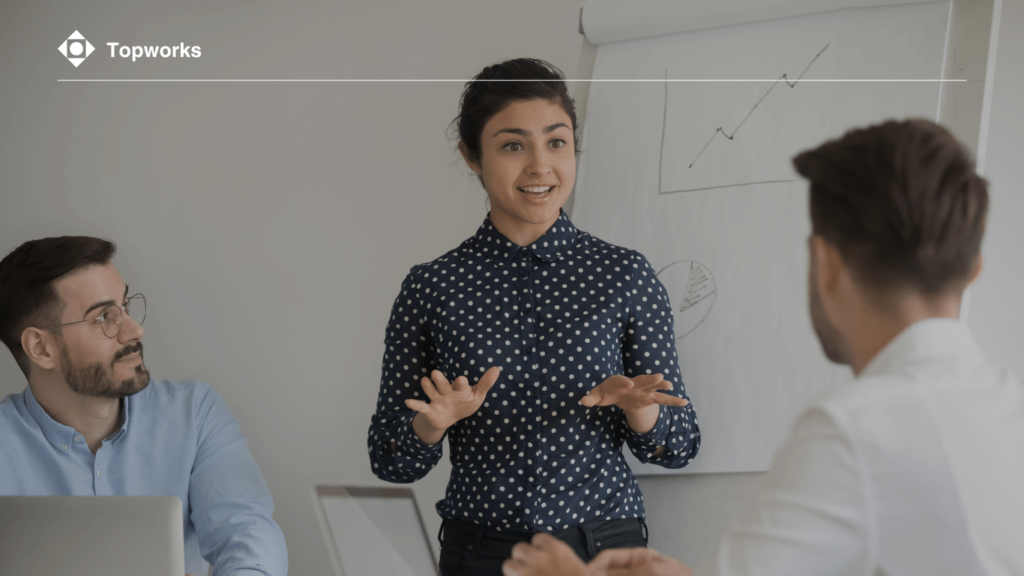
China: The Manufacturing Powerhouse
China maintains its position as the top manufacturer of affordable injection molding solutions which draws global businesses because of its strong benefits. Chinese factories benefit from lower labor expenses than Western territories since they employ skilled workers at competitive prices. The cost savings from manufacturing operations reach between 20% and 60% when compared to North American or European domestic production. Richfields Corporation produces more than 900 molds per year from their Chinese manufacturing facilities with both superior quality standards and economical production.
The substantial production capacity enables cost benefits through economies of scale which benefit clients who need to produce large quantities of products. In spite of their reduced costs many Chinese manufacturers choose to invest heavily in state-of-the-art equipment and automated systems. The innovative strategies at Richfields Plastics merge with affordable solutions to maintain consistent product quality.
Through process optimization, Chinese manufacturers have shortened delivery times even though they operate at distant locations. Manufacturers who enhance their operational speed can minimize some of the difficulties that arise when operating overseas.
India: The Rising Contender
The injection molding industry in India continues to expand rapidly which makes it a competitive choice for manufacturers who seek cost-effective solutions. The Indian market for injection molding machines will expand to USD 888.15 million by 2030 while maintaining a 7.2% annual growth rate starting from its current value of USD 532.94 million in 2023.
The quick growth of the sector demonstrates both rising capabilities and increased investment in this field. The energy efficiency approach of Windsor Machines as an Indian supplier centers on achieving the lowest operating expenses per processed kilogram of polymer which suits manufacturers who need extended production times.
Indian manufacturer DGP Windsor provides low-cost energy-efficient machines alongside extensive after-sales service that resolves a major problem with foreign production. The technical education system of India produces skilled engineers who have improved its injection molding capabilities with enhanced quality and sophistication while preserving cost benefits.
Mexico: The Nearshoring Option
North American businesses find Mexico attractive because it combines cost-effective operations with ideal strategic location. Manufacturing operations in Mexico deliver substantial labor savings to US companies through its well-trained workforce that executes modern manufacturing methods.
A United States company that manufactures in Mexico enjoys faster shipping and shorter delivery times than products from Asia which makes its operations ideal for urgent projects. The commitment to quality standards among Mexican manufacturers provides companies with strict quality control needs an attractive solution due to their competitive prices.
The United States-Mexico-Canada Agreement grants trade benefits which decrease manufacturing costs in Mexico beyond what overseas production can achieve.
Vietnam: The Emerging Alternative
The injection molding industry in Vietnam experienced rapid development which brings forward several distinct benefits to the market. The Vietnam injection molded plastics market will experience continuous growth through a projected 3.60% CAGR from 2024 to 2032 because of steady sector investment and expansion.
The labor costs in Vietnamese manufacturing sites stand among the lowest in Southeast Asia thus delivering Chinese-level price benefits without facing the same level of resource competition. The production facilities at Deluxe Plastics and other Vietnamese facilities provide complete injection molding capabilities in addition to assembly services and secondary operations which enables optimized manufacturing processes and lowers overall expenses.
The leading injection molding companies in Vietnam continue to invest in training alongside technological advancements which results in better operational abilities at competitive prices.
The Selection of a Cost-Effective Manufacturer Requires Several Essential Factors for Evaluation
The following points need examination when selecting potential injection molding partners: A thorough total cost analysis requires businesses to investigate both the listed price and shipping expenses alongside quality control visits and costs related to rework. Quality capabilities require manufacturers to hold specific industry-specific certifications and maintain proper quality control procedures.
The quality of communication channels and English proficiency levels between partners reduces the occurrence of expensive misunderstandings. The protection levels for intellectual property vary across regions so you need to include this aspect in your manufacturing decision. Manufacturers possess different capabilities for producing either large quantities of products or limited specialized runs.
Conclusion
The process of choosing a cost-efficient injection molding factory demands weighing between labor expenses and delivery systems and manufacturing requirements and language capabilities.
Alternative manufacturing sites in India, Mexico, and Vietnam present attractive options to Chinese competitors based on specific production needs. A successful decision-making process involves examining various options throughout different geographical areas while weighing short-term price benefits against longer-term business advantages.
A thorough examination of manufacturing partners and precise cost analysis of production will help you select the best solution that combines superior quality with economical outcomes for your injection molding needs.