Moulding the Future: Latest Trends in Plastics Injection Molding
Greetings! As a seasoned injection molding expert with over 20 years in the plastics industry, I’m thrilled to share my insights on the key trends that are reshaping and revitalizing the field of plastic injection molding. At our company, we pride ourselves on staying ahead of the latest developments and innovations to deliver the most cutting-edge solutions to our clients. The injection molding space is an extremely dynamic one, with new technologies and sustainable solutions emerging every year. In fact, the global injection molded plastics market is projected to reach $513 billion by 2028!
Clearly, this is an industry experiencing immense growth and change. In this blog, I’ll highlight four major trends that are moulding the future of injection molding – from material breakthroughs to automated processes and enhanced design capabilities. By understanding these trends, you can gain valuable intelligence to help future-proof your business. So let’s dive in!
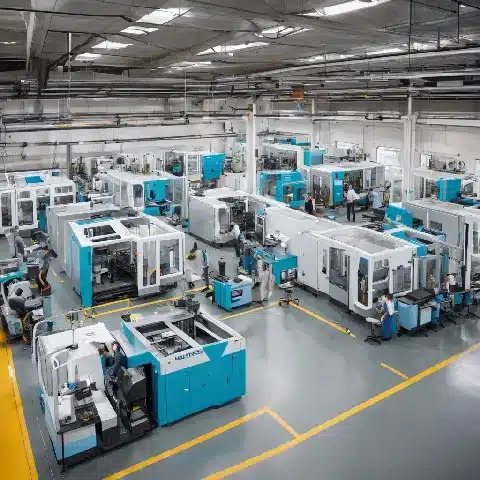
Material Innovations: The Rise of Sustainable Plastics
One of the most impactful trends is the development of novel sustainable and bio-based plastic materials for injection molding. With rising environmental awareness amongst consumers, brands are responding by adopting eco-friendly materials like:
- Polylactic acid (PLA) – Derived from plant starches like corn and potatoes, PLA is a biodegradable polymer growing enormously in popularity. It can produce plastic products with a lower carbon footprint.
- Polyhydroxyalkanoates (PHA) – These biodegradable polyesters are synthesized by microorganisms and offer similar properties to conventional plastics. PHA plastics are renewable and less reliant on fossil fuels.
- Bio-PET – Conventional PET plastic (used for bottles and packaging) is being partially replaced by bio-PET, which incorporates materials from plant-based sources. This reduces environmental impact.
Additionally, high-performance plastics are enabling lightweight, durable components for industries like aerospace, medical, and electronics. Materials like PEEK and PEI expand the design possibilities for injection molded parts.
Ultimately, these material science innovations allow for more sustainable plastic products without compromising on functionality – a win-win for both people and planet!
Tech Revolutionizing the Process: Automation & 3D Printing
Beyond materials, new technologies are also revolutionizing injection molding processes and capabilities. Two prime examples are:
Automated Production
- Robotic arms and AI-powered systems are enhancing efficiency, precision, and consistency in injection molding operations.
- Automated parts handling reduces human errors and minimizes injury risks.
- Intelligent process monitoring enables proactive adjustments before defects occur.
- Overall, automation increases productivity and frees up workers for higher-value tasks.
3D-Printed Molds
- Additive manufacturing (3D printing) facilitates rapid prototyping of injection molds, without the lead time and costs of CNC machining.
- 3D printing enables more complex mold geometries that improve cooling, venting, and part ejection.
- Iterations and design changes can be quickly incorporated, accelerating new product development.
- Low-volume tooling and bridge tooling costs are reduced with 3D-printed molds.
By embracing automation and digital technologies like 3D printing, injection molders can maximize quality and efficiency gains across the entire manufacturing sequence.
Pushing the Boundaries of Design
Injection molding design itself is also evolving to push the boundaries of what’s achievable. Two noteworthy trends are:
Micro-molding
- With micro-molding technology, plastic parts with ultra-fine details down to 0.005 inches can be produced.
- Miniaturized medical devices, electronics components, and precision parts for various industries are being fabricated more accurately.
- Micro-molding expands the capabilities and applications of injection molded plastics.
Multi-Component Molding
- Multi-component molding combines different plastic materials and colors into a single part, eliminating assembly.
- This allows for intricate part designs with overmolded grips, seals, barriers that optimize function.
- Manufacturers can integrate inserts and achieve more dimensional stability.
- The scope for creative, multi-functional product designs is significantly increased.
As evident, innovations in micro-molding and multi-component techniques are removing prior limitations in plastic injection molding and enabling next-generation product designs.
Sustainability in the Spotlight
Lastly, sustainability has taken center stage as a priority across the injection molding sector. Efforts to minimize environmental impacts now define best practices:
- Efficient cooling technology like conformal cooling channels reduces energy consumption and cycle times.
- Closed-loop recycling systems recover, regrind, and reuse plastic waste from the molding process itself.
- Lightweighting by designing thinner walls and optimized geometries cuts down on unnecessary plastic usage.
- Compostable materials derived from plants are being adopted as sustainable options for single-use plastic items.
- Renewable energy usage like solar panels on production facilities also align with eco-friendly motives.
Brands that demonstrate tangible sustainability commitments can boost consumer trust and loyalty in today’s climate-conscious marketplace.
Here is a table summarizing the key trends in plastic injection molding:
Trend | Sub-Trends | Benefits |
---|---|---|
Material Innovations | – Sustainable plastics like PLA, PHA, bio-PET – High-performance polymers | – Reduced environmental impact – Expanded capabilities |
Technology Advancements | – Automation & robotics – 3D printed molds | – Increased efficiency & productivity – Faster prototyping & new design options |
Design Capabilities | – Micro-molding – Multi-component molding | – Ultra-precise, miniaturized parts – Creative, multi-functional products |
Sustainability | – Efficient cooling systems – Closed-loop recycling – Lightweighting – Compostable materials – Renewable energy | – Energy & plastic waste reduction – Lower carbon footprint – Eco-friendly image |
Conclusion: The Future is Now
It’s an incredibly exciting time to be in the injection molding space! As you can see, this industry is brimming with innovation across every aspect – materials, technologies, design techniques and sustainability practices. By embracing these trends and advances, plastic injection molders can deliver higher-performing, ultra-precise and environmentally-friendly solutions. The time is now to leverage these developments and mold a brighter future.
I hope this overview has provided valuable insights into the key trends shaping the plastics injection molding sector today. At our company, we actively incorporate such cutting-edge solutions into all our manufacturing operations and services. Please [get in touch]https://www.company.com/contact]) for a consultation on your project requirements or to learn more about our capabilities. We are always eager to discuss these transformative trends with clients and partners to push the boundaries of possibility together.