Introduction to Injection Molding Cycle Time
When it comes to manufacturing, cycle time is key. It affects production efficiency, cost, lead time and product quality. But what is cycle time and why is it so important?
In simple terms cycle time is the total time from start of the injection molding process to the end of one production cycle, ready for product removal and next cycle.
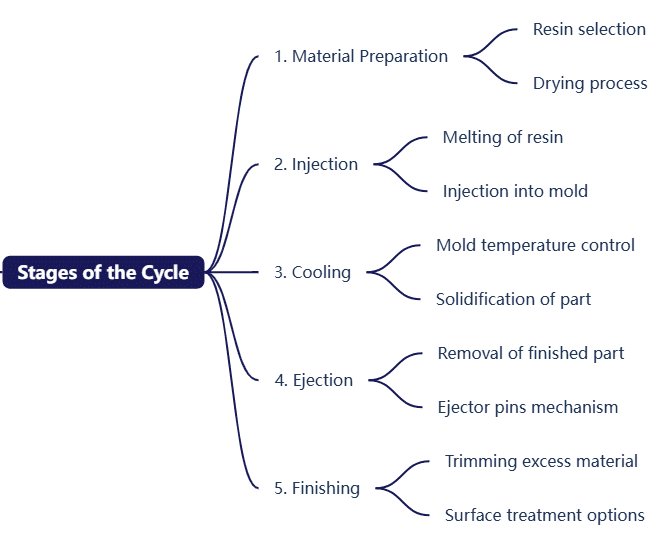
Think of it as the beat of your production line – it determines how fast you can make products and meet market demand. In this article we’ll look at the factors that affect injection molding cycle time, how to measure it and how to optimize it. Let’s get started!
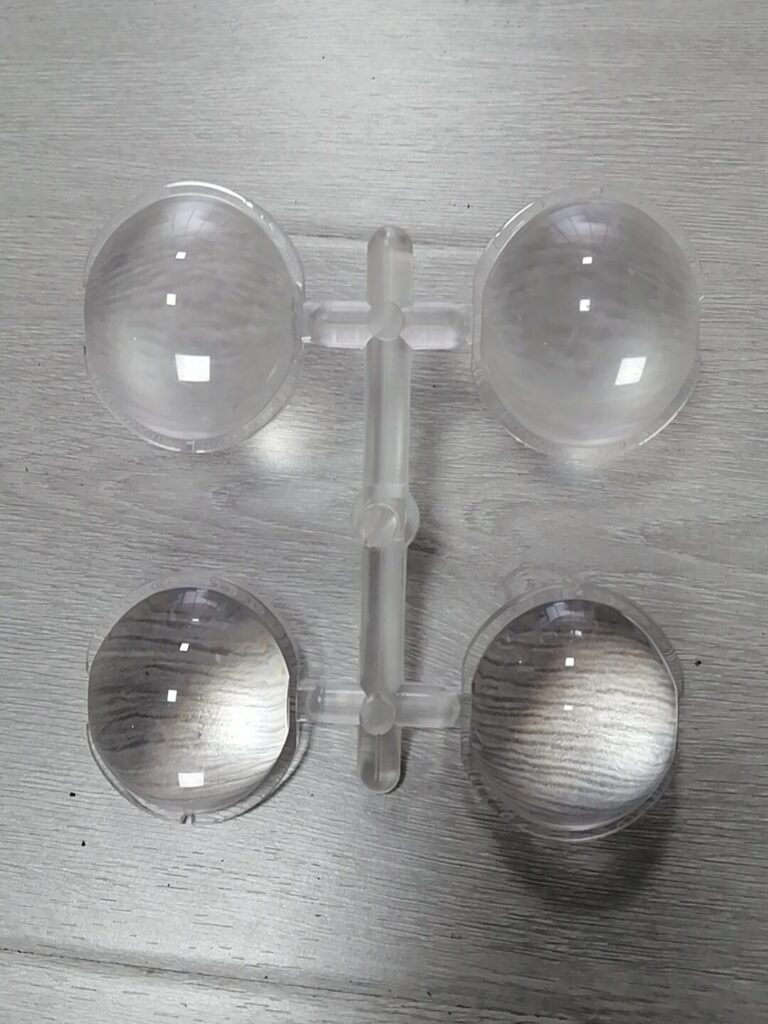
What Affects Cycle Time?
Cycle time is critical for any injection molder. Several factors play a part in how long each cycle takes. Let’s look at them:
1. Material
The type of plastic you use has a big impact on cycle time. Different plastics have different melting points, viscosities and cooling rates. For example polypropylene has a faster cycle time than polycarbonate because of its lower melting point and faster cooling properties.
2. Mold Design
A good mold can be the difference between a short and long cycle time. Complex molds with lots of features or multiple cavities take longer to cycle. Optimizing the mold design for simplicity and efficiency can result in big cycle time reductions.
3. Injection Speed
The speed at which the injection unit fills the mold has a big impact on cycle time. Faster injection speeds mean shorter fill times but can also result in defects like jetting or incomplete filling. Balancing speed with quality is key to minimizing cycle time and product integrity.
4. Cooling Time
Cooling time is the longest part of the cycle. Part thickness, material and mold temperature all affect cooling rates. Techniques like conformal cooling channels can reduce cooling times and overall cycle time.
Cooling time accounts for 80% of the cycle time so it’s critical to design a efficient mold cooling system. An optimized cooling system not only reduces production time but also improves the quality of the final product by reducing defects like warping or shrinkage. Proper placement of cooling channels, selection of right material and advanced cooling techniques like conformal cooling can make a big difference to the process.
5. Temperature Settings
Getting the temperature settings right for the mold and material is critical. Higher temperatures can speed up the melting process for faster injection but can also extend cooling times if not managed properly. Precise temperature control not only gives you optimal cycle times but also product quality, energy consumption and reduced defects during production.
6. Number of Cavities
The number of cavities in the mold directly affects cycle time. Multi cavity molds can produce more parts at once but require careful synchronization and cooling management to avoid extended wait times. Knowing how to balance cavity count with cycle efficiency is key.
Cooling systems
Cooling systems are key in the injection molding process and directly affect production efficiency and part quality. The three main types of cooling systems are water cooled, air cooled and oil cooled.
- Water cooling is the most common because of its high thermal conductivity, allows for fast heat removal from the mold. This method uses chilled water circulating through channels in the mold to pull heat away from the molten material so the material can solidify faster and shorter cycle time. But requires careful design to prevent leaks and manage condensation.
- Air cooled systems are used where water is not available or impractical. These systems use ambient air, often with fans, to cool the mold. Air cooling is simpler and cheaper to implement but results in longer cooling times compared to water cooling because air has lower thermal conductivity.
- Oil cooled systems are also used for larger molds or where rapid cooling is required. They circulate oil through the mold, provides good heat transfer but at a higher operational cost.
In the end, the choice of cooling system depends on many factors like mold complexity, material properties and production requirements. A good cooling system not only reduces cycle time but also minimizes defects in molded parts so it’s a critical consideration for manufacturers who want efficiency and quality in their injection molding process.
Ways to Optimize Cycle Time
Now that we know the factors that affect cycle time, let’s get to the actionable strategies to optimize it for better efficiency and productivity.
Optimize Machine Settings
Tweaking machine parameters like injection speed, pressure and cooling time can reduce cycle time. Experimenting with different approaches will allow teams to find the most efficient way and get consistent results.
Invest in Good Equipment
Modern high performance injection molding machines are designed to be more efficient. Investing in new equipment will make operations simpler and shorter cycle time.
Continuous Improvement Programs
Implementing Lean Manufacturing or Six Sigma will help you identify areas for improvement. Reviewing and refining your process regularly will give you sustainable cycle time improvements.
The Future of Cycle Time in Injection Molding
As technology advances the injection molding world is changing. 3D printing and advanced materials are redefining production time and efficiency. Stay informed on these trends and you’ll be ready to adapt and optimize cycle time.