Custom Plastic Injection Molding 101
In today’s fast paced manufacturing world custom plastic injection molding is a staple. It’s versatile, efficient and cost effective for making high quality plastic products. In this guide we’ll dive into the details of custom plastic injection molding, processes, benefits, applications and more. Whether you’re an engineer or a curious customer this article is a resource for you to learn and make informed decisions.
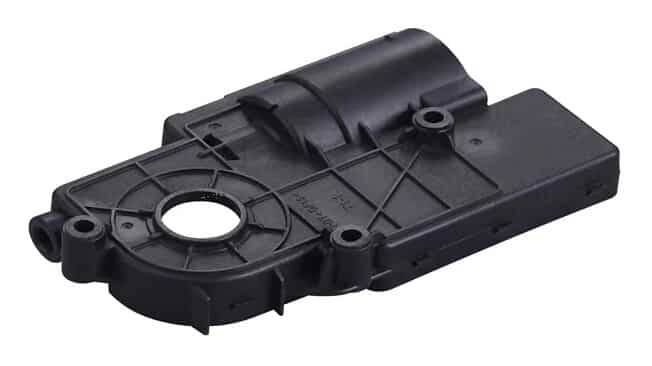
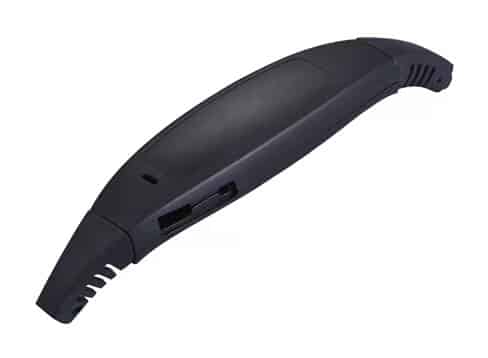

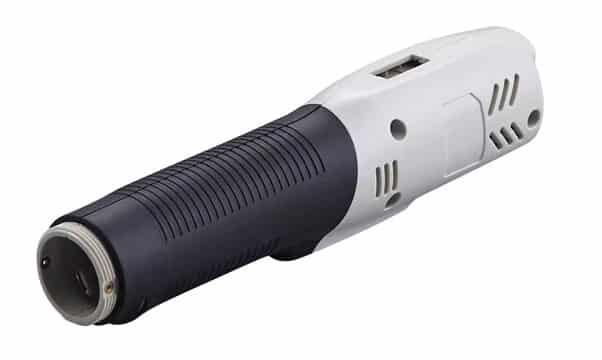
What is Custom Plastic Injection Molding
The Basics
Custom plastic injection molding is a manufacturing process where plastic material is melted and injected into a mold to create intricate shapes and designs. This is ideal for making precise and complex parts with minimal scrap. The process has several stages, clamping, injection, cooling, ejection and can use various plastic materials.
Materials Used
The material used makes a big difference in the end product. Common plastics are:
- – Polyethylene (PE): Durable and flexible for consumer goods.
- – Polypropylene (PP): Chemical resistant for packaging and automotive parts.
- – Acrylonitrile Butadiene Styrene (ABS): Impact resistant for electronic housings.
- – Polycarbonate (PC): Transparent and tough for optical applications.
Knowing the properties of each material helps you choose the right one for your application, balancing cost, strength and thermal stability.
Benefits of Custom Plastic Injection Molding
Speed and Accuracy
One of the biggest benefits of injection molding is speed. The process can produce thousands of identical parts with high accuracy, perfect for mass production. Using CAD and CAM systems ensures each part meets specifications.
Cost
While the initial cost of the mold is high, the cost per unit goes down with large volume production. The high speed and minimal scrap of the process also adds to the cost savings making it economical for many industries.
Design Capabilities
Custom plastic injection molding has unlimited design capabilities. Complex shapes, intricate details and varying wall thicknesses are possible. Plus the ability to use different materials and colors in one mold cycle allows for unique product design and customization.
Industries:
Automotive
In the automotive industry injection molding is used to make components like dashboards, bumpers and interior panels. The ability to make lightweight yet strong parts is key to improving fuel efficiency and vehicle performance.
Consumer Electronics
Injection molding is used in consumer electronics to make durable and lightweight housings, connectors and components. The precision of the process ensures compatibility and functionality of electronic devices.
Medical and Healthcare
The medical industry uses injection molding to make sterile single use medical devices and components like syringes, vials and diagnostic equipment. The ability to use biocompatible and sterilizable materials makes it perfect for medical applications.
Custom Plastic Molder
Things to Consider
When choosing a custom plastic molder, consider:
- – Experience and Knowledge: Companies with a history and expertise in your industry.
- – Technology and Machinery: Companies that invest in latest molding technology can offer better accuracy and speed.
- – Quality Control: Strong quality control process is important to ensure consistency and standard of the product.
- – Customer Service: A company that provides good customer service can make a big difference.
Capabilities
Evaluate the company’s capabilities in mold design, material selection and post processing services. A one stop shop can reduce production time.
Custom Plastic Injection Molding Trends
Sustainability
The trend towards sustainable manufacturing is affecting the injection molding industry. Companies are using recycled materials and energy efficient processes to reduce their environmental footprint. Biodegradable plastics and closed loop recycling systems are becoming more common.
Technology
Technology is changing the future of injection molding. Smart technologies like IoT and AI are enabling real time monitoring and process optimization. Additive manufacturing (3D printing) is being used to make complex mold designs and reduce costs.
Summary
Custom plastic injection molding is a versatile and essential process across many industries. It can make intricate and high quality parts fast and cost effective. As technology advances and sustainability becomes more important, the injection molding industry will continue to evolve and adapt and offer more possibilities and solutions.
Frequently Asked Questions
1. How long does a custom injection molding project take?
Lead time for custom injection molding can vary greatly depending on the complexity of the design volume of production and the company chosen. Generally it can be from a few weeks (from 4 to 8 weeks) to several months.
2. Can recycled materials be used in injection molding?
Yes, recycled materials can be used in injection molding. Many companies are now using post consumer and post industrial recycled plastics to be sustainable and reduce carbon footprint.
3. How does injection molding compare to 3D printing?
Injection molding is more cost effective for high volume production due to its speed and efficiency. 3D printing is more suitable for low volume production and prototyping as it can make complex geometries without the need for molds.
4. What are the common issues in injection molding?
Common issues in injection molding are material selection, mold design complexity and consistency of quality. Solving these issues require expertise, technology and quality control.
5. Is injection molding for my product?
Injection molding is if your product requires high volume of identical parts, complex design or combination of materials and colors. Talk to a molding expert to find out if it’s right for you.