Affordable Injection Molding: Cut Costs, Not Quality
Have you ever wondered why some companies can offer injection molded parts at a fraction of the cost of others? The answer lies in smart, affordable injection molding solutions without compromise. Whether you’re a startup founder or an established manufacturer, knowing these cost saving strategies will change your production economics.
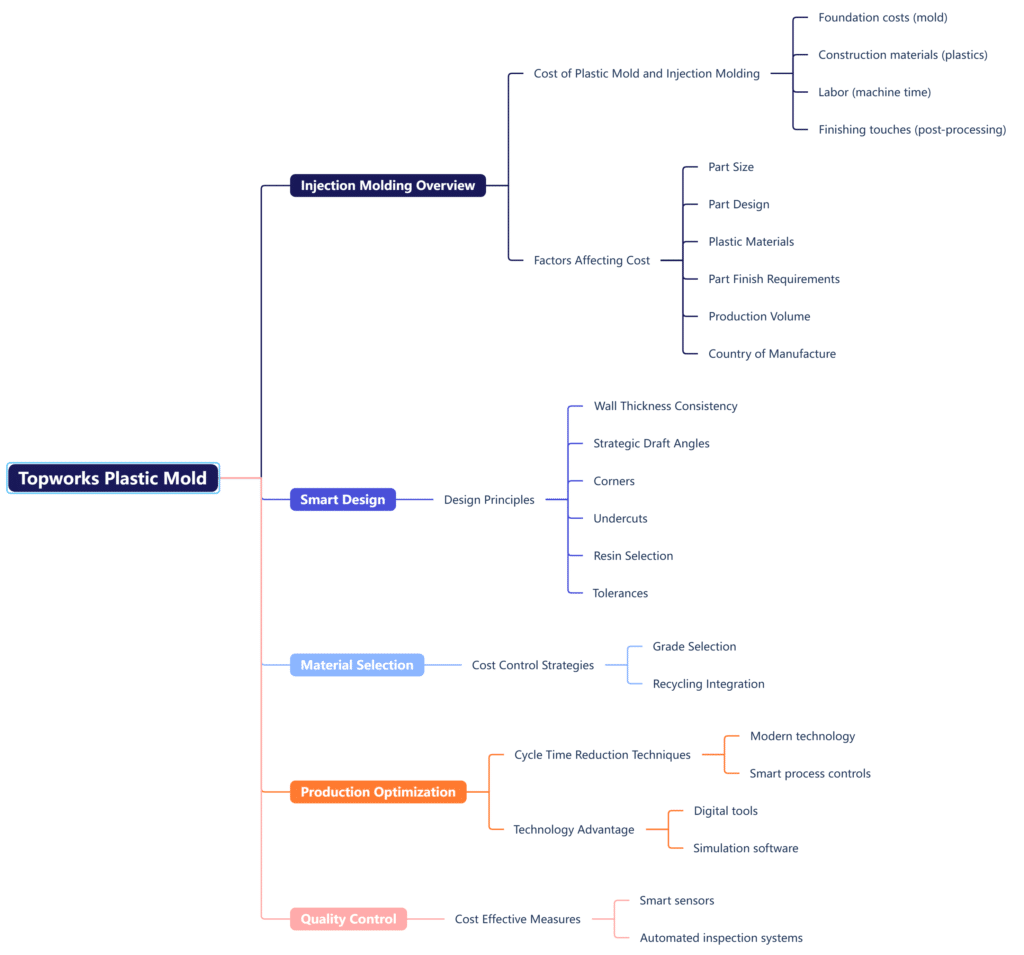
The Real Cost of Injection Molding
Think of injection molding like building a house – you’ve got your foundation costs (the mold), construction materials (plastics), labor (machine time), and finishing touches (post-processing). Just like a smart builder knows where to invest and where to save, successful manufacturers know how to balance these elements to create affordable injection molding solutions.
It’s not about cutting corners, it’s about making smart decisions at every step of the process. Let’s get into how you can make this manufacturing method more affordable without sacrificing the quality your customers expect.
Factors | Description |
---|---|
Part Size | Bigger parts require larger molds, which will increase steel, machining and assembly cost. |
Part Design | Complex parts may require detailed molds with special features, like inserts,sliders and lifters,which affect cost. |
Plastic Materials | Specific materials may necessitate the use of particular mold materials, like POM and PA need stainless steel which PA+GF needs hard surface steel. |
Part Finish Requirements | High gloss surface(mirror surface) requirements may require expensive steel and precise polishing,like S136 or DIN1.2316, which cost is very high. |
Production Volume | Higher volume molds require more cavities and higher-grade steel, like H13,1.2344. |
Country of Manufacture | Different countries have varying labor costs, impacting the overall mold cost. In China, the average cost of an injection mold is approximately 40% less than in Western nations. |
Smart Design: Your First Step to Affordable Molding
You might be surprised to learn that up to 70% of your product’s final cost is determined during the design phase. Just like a chef’s prep determines the success of a meal, your design choices will make or break your budget.
Design Principles That Save Money
When we talk about affordable injection molding solutions, the design stage is where the magic happens. Here are the key elements: Wall Thickness Consistency: Imagine trying to freeze a thick milkshake versus a thin one – thicker sections take longer to cool, just like uneven wall thickness in your parts takes longer to cool and costs more.
Strategic Draft Angles: These are like the slight tilt on a cake pan that helps you remove the cake easily. Proper draft angles reduce production time and tooling wear, which directly impacts your bottom line.
Here is a summary table for injection molding design considerations:
Design Aspect | Considerations |
---|---|
Wall Thickness | does your design meet or exceed the nominal wall thickness? With a consistent wall thickness in the design, will your part cool evenly? |
Draft Angles | What’s your draft angle to the shrinkage you expect during cooling?Can your part be ejected from the mold easily with the draft angles you have? Are you going to stress your mold with your current design? |
Corners | Have the corners been radiused to avoid shrinkage, warping, shearing and/or breakage?How are all corners shaped in the mold so enough material can flow in and a consistent wall thickness is maintained? |
Undercuts | Can you remove any undercuts from the mold design without changing the function of the part?Can the mold be designed to accommodate the undercuts without going over budget? |
Resin Selection | Does the part design allow for proper flow of resin during injection and will it withstand the pressure required? What can affect the part’s cooling time, finish or other properties? How can you resolve those with changes to the part design and/or resin? |
Tolerances | How do your part’s tolerances affect the tooling (i.e. changing material for the mold, needing extra quality checks or more complex molds)? How can you address the performance requirements by redesigning the part/mold? |
Material Selection: The Foundation of Cost Control
Choosing the right material is like selecting ingredients for a gourmet meal – you need the right balance of quality and cost. I’ve seen companies save up to 30% on material costs just by making smart material choices.
Cost Effective Material Strategies
Your material choice impacts not just the part cost but the entire production process. Think about: Grade Selection: Premium materials aren’t always necessary. Often a standard grade can deliver the same performance at a lower cost. Recycling Integration: Including recycled materials can save you a lot of money while maintaining quality – it’s like using perfectly good leftover ingredients in a new recipe.
Production: Where Theory Meets Practice
Production optimization is where theory meets practice. It’s one thing to have a great design and suitable materials, but the real savings come from running your operation like a well oiled machine.
Cycle Time Reduction Techniques
Every second counts in injection molding. Reducing cycle time is like optimizing a busy restaurant’s kitchen – the faster you can serve quality meals the more profitable you become. Modern technology and smart process controls can help you achieve that.
The Technology Advantage
In today’s digital age technology isn’t just an option – it’s a requirement for affordable injection molding solutions. Think of it as having a GPS for your manufacturing process – it helps you avoid costly shortcuts and find the most direct route to your destination.
Digital Tools and Their Impact
Modern simulation software can predict and prevent problems before they happen, so you don’t have to go through trial and error. It’s like having a practice run before the big game – you can identify and fix problems before they cost you money.
Quality Control: The Cost Saving Paradox
Here’s something that might seem counterintuitive: spending money on quality control actually saves you money in the long run. It’s like regular maintenance on your car – pay a little now or pay a lot later.
Cost Effective Quality Measures
Modern quality control doesn’t have to be expensive. With smart sensors and automated inspection systems you can catch defects early and prevent waste.
Future Proof Your Investment
The world of injection molding is changing fast. Stay ahead by being ready for the changes and affordable injection molding solutions for your current needs.
Emerging Technologies and Cost Savings
From artificial intelligence to advanced automation, new technologies are making injection molding more affordable than ever. It’s like having a crystal ball that helps you prepare for future opportunities while optimizing current operations.
Your Business is Unique
Every business is different and what works for one won’t work for another. The key is finding the right balance of affordable injection molding solutions for your business.
Summary
Affordable injection molding solutions isn’t about finding a silver bullet – it’s about a holistic approach that considers design, materials, production and technology. By taking a whole system approach and continuous improvement you can save big and deliver the quality your customers expect.
FAQs
Q1: What’s the biggest cost reducer in injection molding?
The design phase is usually where you can reduce the most costs, as it impacts material usage and production efficiency. Smart design can save up to 70%.
Q2: Am I paying too much for injection molding?
Compare your part costs to industry benchmarks, considering material, part complexity and volume. If you’re paying more than 15-20% above average it’s time to review your process.
Q3: Can small run injection molding be cost effective?
Yes! Modern technology and rapid tooling options have made small run injection molding more affordable than ever. Just choose the right combination of tooling and production strategy for your volume.
Q4: How long is the ROI on new injection molding equipment?
Most companies see ROI in 12-24 months on new, efficient injection molding equipment. But this can vary depending on volume and part complexity.
Q5: How much can I save with affordable injection molding solutions?
Companies typically save 15-30% with cost saving strategies. Some save even more with long term optimization.
This affordable injection molding solutions guide gives you practical tips and actions to save costs and deliver quality. Remember the journey to cost effective manufacturing is continuous – keep learning, adapting and optimizing for best results.